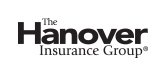
Worker emergency response planning
Failure to prepare for emergencies can result in significant losses to employees and property damage to facilities and the environment. Facilities that have prepared for emergencies have minimized employee deaths, injuries and illnesses, and property damage. This page details the basic steps to handle an emergency in the workplace. The elements of a worker emergency response plan are discussed, including planning, chain of command, communications, accounting of personnel, emergency response teams, training, personal protection, confined space entry and medical assistance.
The information in this report is from a publication of the Occupational Safety and Health Administration, entitled How to Prepare for Workplace Emergencies. It details the basic steps to handle emergencies in the workplace. These emergencies include accidental releases of toxic gases, chemical spills, fires, explosions, and bodily harm and trauma caused by workplace violence.
Planning
The effectiveness of response during emergencies depends on the amount of planning and training performed beforehand. Management should show its support for plant safety programs and the importance of emergency planning. If management is not interested in employee protection and in minimizing property loss, little can be done to promote a safe workplace. It is therefore management's responsibility to see that a program is instituted and that it is frequently reviewed and updated. The input and support of all employees should be obtained to ensure an effective program. The emergency response plan should be developed locally and should be comprehensive enough to deal with all types of emergencies specific to that site.
The emergency response plan, at a minimum, should include the following elements:
- Emergency evacuation procedures and assignments.
- Essential facility operations (or shut down) procedures for employees who remain before the plant is evacuated.
- Post-emergency accounting of employees' procedures.
- Search and rescue and medical procedures.
- Emergency reporting and notification procedures.
- Employee names/job titles or departments to be contacted for additional information or explanation of emergency response plan assignments.
The scope of the emergency action plan should include all potential emergencies that can be expected in the workplace. Therefore, it will be necessary to perform a hazard audit to determine toxic materials in the workplace, hazards, and potentially dangerous conditions. For information on chemicals, the manufacturer or supplier can be contacted to obtain Material Safety Data Sheets (MSDSs). These forms describe the hazards that a chemical may present, list precautions to take when handling, storing, or using the substance, and outline emergency and first-aid procedures.
The employer should list in detail the procedures to be taken by those employees who remain behind to care for essential facility operations until their evacuation becomes absolutely necessary. This may include monitoring facility power supplies, water supplies, and other essential services that cannot be shut down for every emergency alarm, and use of fire extinguishers.
For emergency evacuation, the use of floor plans or workplace maps that clearly show the emergency escape routes and safe or refuge areas should be included in the plan. All employees should be advised of what actions they are to take in emergency situations that may occur in the workplace, such as a designated meeting location after evacuation. The plan should be reviewed with employees initially when the plan is developed, whenever employees' responsibilities under the plan change, and whenever the plan is changed. A copy of the plan should be kept where employees can refer to it at convenient times.
Chain of command
A chain of command should be established to minimize confusion so that employees will have no doubt about who has authority for making decisions. Responsible individuals should be selected to coordinate the work of the Emergency Response Team. In larger organizations, this may be a coordinator in charge of overall operations, public relations, and ensuring that outside aid is attained.
Because of the importance of these functions, adequate backup should be arranged so that trained personnel are always available. The duties of the Emergency Response Team Coordinator should include the following:
- Assessing the situation and determining whether an emergency exists that requires activating the emergency procedures.
- Directing all efforts in the area, including evacuating personnel.
- Ensuring that outside emergency services, such as medical aid and local fire departments, are called in when necessary.
- Directing the shutdown of plant operations when necessary.
Communications
During a major emergency involving a fire or explosion it may be necessary to evacuate offices in addition to manufacturing areas.
Also, normal services, such as electricity, water, and telephones, may be nonexistent. Under these conditions, it may be necessary to have an alternate area to which employees can report or that can act as a focal point for incoming and outgoing calls. Since time is an essential element for adequate response, the person designated as being in charge should make this the alternate headquarters so that he/she can be easily reached.
Emergency communications equipment, such as amateur radio systems, public address systems, or portable radio units should be present for notifying employees of the emergency and for contacting local authorities.
A method of communication also is needed to alert employees to the evacuation or to take other action as required in the plan. Alarms should be audible or seen by all people in the facility and have an auxiliary power supply in the event electricity is affected. The alarm should be distinctive and recognizable as a signal to evacuate the work area or perform actions designated under the emergency action plan. Management should explain to each employee the means for reporting emergencies, such as manual pull box alarms, public address systems, or telephones. Emergency phone numbers should be posted on or near telephones, on employees' notice boards, or in other conspicuous locations. The warning plan should be in writing and management should ensure that each employee knows what it means and what action should be taken.
It may be necessary to notify other key personnel, such as the facility manager or physician, during off-duty hours. An updated documented list of key personnel, listed in order of priority, should be kept.
Accounting for personnel
Management will need to know when all personnel have been accounted for. This can be difficult during shift changes or when contractors are on site. A responsible person in the control center should be appointed to account for personnel and to inform police or Emergency Response Team members of those persons believed missing.
Emergency response teams
Emergency Response Teams are the first line of defense in emergencies. Before assigning personnel to these teams, the employer should assure that employees are physically capable of performing the duties that may be assigned to them. Depending on the size of the facility there may be one or several teams trained in the following areas:
- Use of various types of fire extinguishers.
- First aid, including cardiopulmonary resuscitation (CPR).
- Shutdown procedures.
- Evacuation procedures.
- Chemical spill control procedures.
- Confined space entry procedures.
- Use of self-contained-breathing-apparatus (SCBA).
- Search and emergency rescue procedures.
- Incipient and advanced stage firefighting.
- Trauma counseling.
The type and extent of the emergency will depend on the facility operations and the response will vary according to the type of process, the material handled, the number of employees, and the availability of outside resources. OSHA's Hazard Communication Standard (29 CFR part 1910.1200) is designed to ensure that the hazards of all chemicals produced or imported are evaluated and that information concerning their hazards is transmitted to workers. This is accomplished by means of comprehensive hazard communication programs involving container labeling and other forms of warning, material safety data sheets, and employee training. Emergency Response Teams should be trained in the types of possible emergencies and the emergency actions to be performed.
They are to be informed about special hazards, such as storage and use of flammable materials, toxic chemicals, radioactive sources, and water-reactive substances, to which they may be exposed during emergencies. It is important to determine when not to intervene. For example, team members should be able to determine if a chemical spill is too large for them to handle or whether search and rescue activities should be performed. If there is the possibility of members of the Emergency Response Team receiving fatal or severe injuries, they should wait for professional assistance.
For additional hazard communication information, refer to Occupational Safety Technical Report OS-20-12, Hazard Communication.*
Information regarding OSHA Standard 29 CFR 1910.1200 Hazard Communication, is available at www.osha.gov
For additional Emergency Response Team information, refer to Fire Protection Technical Report FP-45-20, Emergency Response Teams.*
Training
Training is important for the effectiveness of an emergency response plan. Before implementing an emergency action plan, a sufficient number of persons should be trained to assist in the safe and orderly evacuation of employees. Training for each type of disaster response is necessary so that employees know what actions are required.
In addition to specialized training for Emergency Response Team members, all employees should be trained in the following:
- Evacuation plans.
- Alarm systems.
- Reporting procedures for personnel.
- Shutdown procedures.
These training programs should be provided as follows:
- Initially when the plan is developed.
- For all new employees.
- When new equipment, materials, or processes are introduced.
- When procedures have been updated or revised.
- When exercises show that employee performance should be improved.
- At least annually.
The emergency control procedures should be written in concise terms and be made available to all personnel. Drills should be held for all personnel at random intervals at least annually, and an evaluation of performance made immediately by management and employees. When possible, drills should include groups supplying outside services, such as police and fire departments, and emergency medical departments. In buildings containing several places of employment, the emergency response plans should be coordinated with other companies and employees in the building. Finally, the emergency response plan should be reviewed periodically and updated to contain adequate response personnel and program efficiency.
Personal protection
Effective personal protection is essential for any person who may be exposed to potentially hazardous substances. In emergency situations, employees may be exposed to a wide variety of hazardous circumstances, including:
- Chemical splashes or contact with toxic materials.
- Falling objects and flying particles.
- Unknown atmospheres that may contain toxic gases, vapors or mists, or inadequate oxygen to sustain life.
- Fires and electrical hazards.
- Violence in the workplace.
Personal protective equipment
It is extremely important that workers be adequately protected in emergency situations. Some of the safety equipment that may be used includes:
- Eye protection, such as safety glasses, goggles, or face shields.
- Head and foot protection, such as hard hats and safety shoes.
- Proper respirators for breathing protection.
- Whole body coverings, such as chemical suits, gloves, hoods, and boots for body protection from chemicals.
- Body protection for abnormal environmental conditions, such as extreme temperatures.
The equipment selected is required to meet OSHA standards or a nationally recognized standards-producing organization.
For additional personal protective equipment information, refer to the following:
- Occupational Safety Report OS-70-02,
Personal Protective Equipment.* - Occupational Safety Report OS-70-11,
Occupational Eye and Face Protection.* - Industrial Hygiene Report IH-20-03,
Respiratory Protection.*
Information regarding OSHA Standard 29 CFR 1910.132 Personal Protective Equipment, is available at www.osha.gov
Confined space entry
Emergency situations may involve entering confined spaces to rescue workers who are overcome by toxic compounds or who lack oxygen. These OSHA permit-required confined spaces include pits, vaults, tanks, sewers, pipelines, and vessels. Entry into permit-required confined spaces can expose employees to a variety of hazards, such as toxic gases, explosive atmospheres, oxygen deficiency, electrical hazards, and hazards created by mixers and impellers that have not been deactivated and locked out. Personnel should never enter a permit-required confined space unless the atmosphere has been tested for adequate oxygen, combustibility, and toxic substances. Conditions in a permit-required confined space are to be considered immediately dangerous to life and health unless shown otherwise. If a permit-required confined space is to be entered in an emergency, the following precautions are to be adhered to:
- All lines containing inert, toxic, flammable, or corrosive materials are to be disconnected or blocked off before entry.
- All impellers, agitators, or other moving equipment inside the vessel is required to be locked out.
- Employees should wear appropriate personal protective equipment before entering the vessel. Mandatory use of full body safety harnesses is to be stressed.
- Rescue procedures are to be specifically designed for each entry. A trained stand-by person is required to be present. This person should be assigned a fully charged, positive-pressure, self-contained breathing apparatus with a full face piece. The stand-by person is required to maintain unobstructed lifelines and communications to all workers within the permit-required confined space and be prepared to summon rescue personnel if necessary. The stand-by person should not enter the confined space until adequate assistance is present. While awaiting rescue personnel, the stand-by person may make a rescue attempt utilizing lifelines from outside the permit-required confined space.
Medical assistance
Provisions for medical treatment are to be organized in advance of an emergency in order to provide proper care for injured workers:
- In the absence of an onsite medical department or infirmary/hospital in close proximity to the workplace that can be used for treatment of all injured employees, a person or persons trained to render first aid should be provided.
- When the eyes or body of an employee may be exposed to injurious corrosive materials, eye and body washes should be provided for drenching and flushing of the eyes and body.
- Management should ensure the ready availability of medical personnel for advice and consultation on matters of employees' health. This does not mean that health care is to be provided, but rather that, if health problems develop in the workplace, medical help will be available to resolve them.
The following actions should be considered to meet the above requirements:
- Survey the medical facilities near the work-place and make arrangements to handle routine and emergency cases. A written emergency medical procedure should then be prepared for handling accidents with minimum confusion.
- If a workplace is located far from medical facilities, at least one and preferably more employees on each shift are to be trained to render first aid.
- First-aid supplies should be provided for emergency use. This equipment should be ordered through consultation with a physician.
- Emergency phone numbers should be posted in conspicuous places near or on telephones.
- Sufficient ambulance services should be available to handle any emergency. This requires advance contact with ambulance services to ensure they become familiar with facility location, access routes, and hospital locations.
Security
During an emergency, it is often necessary to secure the area to prevent unauthorized access and to protect vital records and equipment.
An off-limits area should be established by cordoning off the area with ropes and signs. It may be necessary to notify local law enforcement personnel or to employ private security personnel to secure the area and prevent the entry of unauthorized personnel.
Certain records (computer and paper) may also need to be protected, such as essential accounting files, legal documents, and lists of employees' relatives to be notified in case of emergency. These records may be stored in duplicate outside the facility or in protected secure locations within the facility.
Additional information
For additional information regarding fire prevention emergency planning, refer to Fire Prevention Technical Report FP-45-15, Fire Prevention Plans.*
Summary
The information contained in this page is provided to assist management in establishing an effective workplace emergency response plan. This page only contains the basic components of an emergency response plan and a more comprehensive plan may need to be developed depending on the nature of the operations contained within the facility. By following the basic emergency response plan elements discussed in this page, injuries and illnesses and property damage should be minimized.
References
- American Insurance Services Group. Engineering and Safety Service. Fire Protection Report FP-45-10, Emergency Action Plans. New York, NY: ISO Services, Inc.
- Occupational Safety and Health Administration. United States Department of Labor. How to Prepare for Workplace Emergencies. Washington D.C.: OSHA 3088. 1995 (Revised).
- ---. Occupational Safety and Health Standards 29 CFR 1910. Washington D.C.: OSHA. 1999.
Copyright ©2001, ISO Services, Inc.
To learn more about Hanover Risk Solutions, visit hanoverrisksolutions.com
The recommendation(s), advice and contents of this material are provided for informational purposes only and do not purport to address every possible legal obligation, hazard, code violation, loss potential or exception to good practice. The Hanover Insurance Company and its affiliates and subsidiaries ("The Hanover") specifically disclaim any warranty or representation that acceptance of any recommendations or advice contained herein will make any premises, property or operation safe or in compliance with any law or regulation. Under no circumstances should this material or your acceptance of any recommendations or advice contained herein be construed as establishing the existence or availability of any insurance coverage with The Hanover. By providing this information to you, The Hanover does not assume (and specifically disclaims) any duty, undertaking or responsibility to you. The decision to accept or implement any recommendation(s) or advice contained in this material must be made by you.
LC MAR 2019 2016-400
171-10016 (10/16)