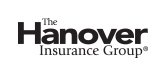
Vehicle inspection
Regardless of the size of the vehicle operated, vehicle inspection is critical for assuring that a motor vehicle is in good enough condition to be driven safely. This report addresses pre-trip, on-the-road, post-trip, and periodic inspections.
Introduction
Inspection is the first line of defense in assuring that a motor vehicle is in a safe operating condition. Finding and repairing a defect or deficiency reduces the risk of a mechanical failure, which can contribute to an accident or vehicle breakdown that results in death, injury, and property damage, as well as missed deliveries, bad publicity, customer dissatisfaction, on-the-road repair problems, or overtime pay for drivers and mechanics.
All operators of motor vehicles should have an inspection system included in their overall safety program. Operators of larger vehicles (i.e., trucks and buses) will likely need to meet minimum federal or state regulations for their inspection program. Drivers are frequently held responsible for vehicle inspection, as drivers spend the greatest amount of time with a vehicle, and they should be trained on how to perform a vehicle inspection and how to describe any problems discovered.
ANSI/ASSE Z15.1, Safe Practices for Motor Vehicle Operations, a voluntary standard approved by the American National Standards Institute (ANSI), requires that organizations have a system in place to ensure that vehicles are inspected on a regular basis and that visual checks be made by drivers each time they operate a vehicle.
Vehicle inspection includes pre-trip, on-the-road, post-trip, and periodic inspections, which are addressed in this report.
Pre-trip inspection
Regardless of the type of vehicle, a driver’s first line of defense in helping to assure a successful trip is to perform a pre-trip inspection. For larger operations, a detailed inspection may be performed by the motor carrier’s maintenance department, but the driver should still try to assure that the vehicle is ready for the road.
The depth of a pre-trip inspection will depend on the size of the vehicle being operated and regulations to which the driver or motor carrier may be subject. Forms to guide drivers in performing a systematic, thorough vehicle inspection are readily available for trucks. Companies operating smaller vehicles can easily develop a report form to help the driver inspect the vehicle properly. Sample vehicle inspection forms are available in the following, which can be found on the Risk Solutions website: Pre-trip inspection of automobiles, vans, and light trucks; Pre-trip inspection of medium-duty straight trucks; Pre-trip inspection of heavy-duty straight trucks; Pre-trip inspection of tractor-trailer units; and Pre-trip inspection of school buses.
Drivers subject to the Federal Motor Carrier Safety Regulations (FMCSR), or to state regulations adopting the FMCSR (generally for vehicles over 10,000 GVWR), are required to be satisfied that the following parts and accessories are in good working order:
- Service brakes, including trailer brake connections
- Parking (hand) brake
- Steering system
- Lighting devices and reflectors
- Tires
- Horn
- Windshield wipers
- Rearview mirrors
- Coupling devices
- Emergency equipment
- Cargo securement devices
While a written pre-trip inspection report is not required by the FMCSR, the use of one will help assure that the driver performs a thorough inspection.
Also for motor carriers subject to the FMCSR, or to state regulations adopting the FMCSR, drivers are required to review the last Driver’s Vehicle Inspection Report, which the FMCSR require to be carried in the vehicle, before driving the vehicle. If defects or deficiencies were noted by the driver who prepared the report, the current driver must sign the report to acknowledge that he/she has reviewed it and that there is a certification that the required repairs have been performed.
On-the-road inspection
Drivers should take a few minutes (e.g., when they park their vehicle for deliveries and rest stops) to make a quick visual check of the vehicle’s condition and load securement devices. Situations such as tires losing air or lights failing may arise while in transit. In addition, checking around the vehicle helps assure that conditions have not changed since the vehicle was parked (e.g., a closely parked vehicle).
Drivers subject to the FMCSR, or to state regulations adopting the FMCSR, must check cargo securement devices within the first 50 miles after beginning a trip and cause any adjustments to be made to the cargo or load securement devices, as necessary, including adding more securement devices, to ensure that cargo cannot shift within or fall from the vehicle. In addition, reexamination and any necessary adjustments must be made whenever:
- The driver makes a change of his/her duty status; or
- The commercial motor vehicle has been driven for three hours; or
- The commercial motor vehicle has been driven for 150 miles, whichever occurs first.
Trucks and buses are subject to on-the-road vehicle inspections by Federal Motor Carrier Safety Administration (FMCSA) inspectors and state officials. If a serious deficiency is noted during the inspection, the vehicle may be placed out-of-service at the inspection site and the motor carrier required to make on-the-road repairs, before the vehicle is allowed to continue travel.
To afford consistency in roadside inspections across North America, the Commercial Vehicle Safety Alliance (CVSA) was formed in 1982. CVSA is an international not-for-profit organization comprised of local, state, provincial, territorial, and federal motor carrier safety officials, as well as allied industry representatives, from the United States, Canada, and Mexico. Its goals are promoting uniformity, compatibility, and reciprocity of commercial vehicle inspections and enforcement activities throughout North America, and providing guidelines for inspection procedures and the training of inspectors. The CVSA publishes, annually, the North American Standard Out-of-Service Criteria (OOSC), which is effective April 1 through March 31 of each year.
CVSA inspection criteria are in alignment with the requirements of the FMCSR. The CVSA may issue an inspection decal, upon satisfactory completion of its Level I, North American Standard Inspection (Vehicle and Driver(s)) or Level V, Vehicle-Only Inspection, which is valid for a maximum of three months. In general, vehicles displaying a valid CVSA decal will not be subject to re-inspection. However, if an obvious defect is noticed on a vehicle with a current CVSA decal, nothing prevents the re-inspection of the vehicle. The CVSA decal criteria apply only to the condition of the vehicle, not the driver. It is possible for a driver to be out-of-service and still have vehicle(s) qualify for a CVSA decal.
Post-trip inspection
Drivers subject to the FMCSR are required to perform a post-trip inspection of the vehicle they operated, except for motor carriers operating only one vehicle, and note any deficiencies with the vehicle or the fact that there are no deficiencies. The report must be in writing and signed by the driver. This driver’s vehicle inspection report must cover at least the following parts and accessories:
- Service brakes including trailer brake connections
- Parking (hand) brake
- Steering system
- Lighting devices and reflectors
- Tires
- Horn
- Windshield wipers
- Rearview mirrors
- Coupling devices
- Wheels and rims
- Emergency equipment
Periodic inspection
Many states have periodic inspection requirements for all vehicles. The FMCSR require motor carriers to have every commercial motor vehicle subject to its control inspected at least once every 12 months. Periodic inspection should identify those vehicle components that are in need of attention, either immediately or in the near future. The minimum periodic inspection standards are contained in Appendix G of the FMCSR.
For motor carriers subject to the FMCSR or in those states adopting the regulations, the term commercial motor vehicle includes each vehicle in a combination vehicle. For example, for a “tractor semitrailer, full trailer combination,” the tractor, semitrailer, and the full trailer (including the converter dolly if so equipped) must each be inspected.
Documentation of vehicle inspection must be carried on the vehicle. This can be either the mandated inspection report or other forms of documentation based on the inspection report, such as a sticker or decal, which contains the following information:
- The date of the inspection
- Name and address of the motor carrier or other entity where the inspection report is maintained
- Information uniquely identifying the vehicle inspected, if not clearly marked on the motor vehicle
- A certification that the vehicle in fact passed the required inspection
A motor carrier may choose to conduct its own inspection, or have a commercial garage, fleet leasing company, truck stop, or other similar commercial business perform the inspection as its agent in states that do not have a mandatory state inspection program meeting federal requirements.
Inspector qualifications
Where a state vehicle inspection program does not exist, a motor carrier must assure that the individual performing the annual inspection is qualified, as follows:
- Understands the inspection criteria and can identify defective components
- Knows the proper methods, procedures, tools, and equipment used in performing the inspection
- Has sufficient knowledge and/or experience to perform an inspection through completion of a state- or federally-sponsored training program, or has earned a certificate from a state or Canadian province to perform inspections or has a combination of training or experience totaling at least one year.
Evidence of the inspector’s qualifications must be retained by the motor carrier during the time that the inspector is performing annual inspections and for one year thereafter.
Recordkeeping requirements
The inspector performing the inspection must prepare a report that identifies:
- The individual performing the inspection
- The motor carrier operating the vehicle
- The date of the inspection
- The vehicle inspected
- The vehicle components inspected, with an indication of the results of the inspection including those components not meeting the minimum inspection criteria
The inspector must certify the accuracy and completeness of the inspection as complying with the regulations. The original or a copy of the inspection report must be retained where the vehicle is either housed or maintained, including reports of inspections performed through a state or other jurisdiction’s roadside inspection program, or by the motor carrier or other entity responsible for the inspection, for 14 months following the inspection, and be available for review upon demand by an authorized federal, state, or local official.
References
- American Society of Safety Engineers (ASSE). Safe Practices for Motor Vehicle Operations. ANSI/ ASSE Z15.1. Des Plaines, IL: ASSE, 2006.
- Commercial Vehicle Safety Alliance (CVSA). February 21, 2010. http://www.cvsa.org.
- Engineering and Safety Service. Commercial Vehicle Report CV-50-12. FMCSR — Driving of Commercial Motor Vehicles. Jersey City, NJ: ISO Services, Inc., 2004.
- —. Commercial Vehicle Report CV-50-16. FMCSR — Inspection, Repair, and Maintenance. Jersey City, NJ: ISO Services, Inc., 2004.
- Federal Motor Carrier Safety Administration. Federal Motor Carrier Safety Regulations. 49 CFR 390-396. U.S. Department of Transportation. February 21, 2010. https://www.fmcsa.dot.gov/regulations/title49/section/390.5
Copyright ©2010, ISO Services Properties, Inc.
To learn more about Hanover Risk Solutions, visit hanoverrisksolutions.com
The recommendation(s), advice and contents of this material are provided for informational purposes only and do not purport to address every possible legal obligation, hazard, code violation, loss potential or exception to good practice. The Hanover Insurance Company and its affiliates and subsidiaries ("The Hanover") specifically disclaim any warranty or representation that acceptance of any recommendations or advice contained herein will make any premises, property or operation safe or in compliance with any law or regulation. Under no circumstances should this material or your acceptance of any recommendations or advice contained herein be construed as establishing the existence or availability of any insurance coverage with The Hanover. By providing this information to you, The Hanover does not assume (and specifically disclaims) any duty, undertaking or responsibility to you. The decision to accept or implement any recommendation(s) or advice contained in this material must be made by you.
LC MAR 2019-105
171-1164 (4/15)