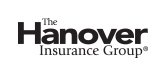
Product safety standards
A standard is a set of characteristics or quantities that describe features of a product, process, service, interface or materials. Standardization is useful for product safety management and product liability prevention. Standards may provide useful information to product designers, and promote a uniform level of safety between similar products. This level of safety may be used when judging the reasonableness of the actions taken by different product manufacturers. Conformance to standards is also useful in evaluating the degree of control that a manufacturer has over its production operations. This report provides information about the U.S. standards-making process, and the benefits and limitations of standards with respect to product safety and product liability.
Product manufacturers frequently incorporate product safety standards into their product designs. These standards may define the way that a product is to perform or detail specific product characteristics. The standard may be developed internally by the manufacturer or by an independent standards developer.
Standardization is useful for product safety management and product liability prevention. Standards may alert designers to potential safety problems that they might not have considered and may promote a uniform level of safety between similar products. This level of safety may be used when judging the reasonableness of the actions taken by different product manufacturers. Conformance to stated requirements is also useful in evaluating the degree of control that a manufacturer has over its production operations.
This report provides information about the U.S. standards-making process and the benefits and limitations of standards with respect to product safety and product liability. For information on international or European standardization activities, see E&S Product Safety Reports PS-10-71, International Standards Organizations, and PS-10-72, European Standards Organizations.
Definition of standard
There are numerous formal definitions for the term “standard.” One widely used definition, from the joint International Organization for Standardization (ISO) and International Electrotechnical Commission (IEC) publication ISO/IEC Guide 2: 2004, Standardization and Related Activities – General Vocabulary, is:
“A document, established by consensus and approved by a recognized body, that provides for common and repeated use, rules, guidelines or characteristics for activities or their results, aimed at the achievement of the optimum degree of order in a given context.”
In U.S. Office of Management and Budget (OMB) Circular A-119, Federal Participation in the Development and Use of Voluntary Consensus Standards and in Conformity Assessment Activities (revised 1.22.2016), the term “standard” includes all of the following:
“(i) common and repeated use of rules, conditions, guidelines or characteristics for products or related processes and production methods, and related management systems practices;
(ii) the definition of terms; classification of components; delineation of procedures; specification of dimensions, materials, performance, designs, or operations; measurement of quality and quantity in describing materials, processes, products, systems, services, or practices; test methods and sampling procedures; formats for information and communication exchange; or descriptions of fit and measurements of size or strength; and
(iii) terminology, symbols, packaging, marking or labeling requirements as they apply to a product, process, or production method.”
These definitions show the broad range of uses and meanings of the term. A more useful, working definition of a standard is simply “a set of characteristics or quantities that describe features of a product, process, service, interface or material.”[6]
Types of standards
Standards may be classified several different ways. They may be classified by their purpose, their intended audience or developer or by the way by which they specify requirements. Also, standards may be classified based upon whether compliance with the standard is voluntary or mandatory. The following sections describe several aspects of these classification schemes.
Purpose
Standards may be used for a variety of purposes. They may be used to define fundamental concepts, such as terminology, metrology (i.e., units of measurement), signs and symbols, conventions, etc. They may be used to define the test methods and analyses that will be used to measure a specific product characteristic. They may be used to define product characteristics or specific performance thresholds that must be reached, such as safety requirements, interoperability requirements or basic fitness for use.
Mandatory versus voluntary standards
Mandatory standards are standards that have been published as part of a code, rule or regulation by a regulatory government body. Manufacturers are legally obligated to comply with these standards and will receive governmental sanctions (e.g., fines, confiscation of product, or imprisonment) if they do not comply. An example of a mandatory standard is the U.S. Consumer Products Safety Commission (CPSC) flammability standard for fabrics used in clothing, which is codified in Title 16 of the Code of Federal Regulations Part 1116 (16 CFR 1116). This standard provides methods of testing and rating the flammability of textiles and textile products for clothing use. See E&S Product Safety Report PS-90-20, Wearing Apparel, for more information about this standard.
A voluntary standard is a standard that may be used at the discretion of the product manufacturer and the lack of use will not result in governmental sanction. Voluntary standards may be developed by individual companies, industry groups, or by key market participants. They may be developed by formal procedures or may be informal standards that become adopted by the marketplace. When voluntary standards are formally derived by a consensus of key market participants, they are called voluntary consensus standards. It has been estimated that there are approximately 50,000 current voluntary standards in the United States that have been developed by more than 600 organizations.[3]
Voluntary standards may attain the effect of mandatory standards if they are referenced in codes and standards adopted by government bodies. The National Electrical Code (NEC) is an example of this. A private organization, the National Fire Protection Association (NFPA), develops and maintains the NEC for use by its members. It has been adopted as a regulatory requirement by all states, making compliance with the standard mandatory. The National Institute for Standards and Technology developed an online database of voluntary standards that have been incorporated by reference in federal regulations. The database is available online at https://www.nist.gov/standardsgov/what-we-do/federal-policy-standards/sibr. Many of these standards are available for viewing online via the IBR Standard Portal.
A good description of the practical difference between mandatory and voluntary standards is the following: “A voluntary standard indicates the lowest safety level that an industry or manufacturer tends to meet in the product it supplies. A mandatory standard indicates the lowest safety level that the government will accept.”[4]
Design versus performance
Design standards, which are also called specification standards, are standards that define product characteristics in terms of how it is to be constructed. For example, the standard may include the dimensions of the product, the materials that must be used, the finish that must be provided, specific precautionary labeling, or other detailed criteria that must be met for the product to conform to the standard. Manufacturers must build their products according to these specific requirements conform to the standard.
Performance standards are standards that define a product’s characteristic in terms of how it is to function and defer to the designer the issue of how to achieve this functionality. For example, the standard might require that a product be designed to withstand a certain imposed force, but not specify a specific method for achieving this requirement. Because performance standards provide fewer restrictions than design standards, they are considered less restrictive to product innovation.
Standards developers
In the United States, both governmental agencies and nongovernment organizations develop standards. In addition to the developers themselves, many other groups participate in standards’ development and dissemination.
Government agencies
The National Institute for Standards and Technology (NIST) identified 80 federal government agencies involved with developing standards in 1996. The Department of Defense (DOD) was the most prolific developer and was responsible for over three-quarters of all the standards.
The recent trend has been for federal agencies to adopt standards prepared by nongovernment groups, rather than preparing or revising their own work. Congress promoted this effort through the enactment of the National Technology Transfer and Advancement Act of 1996 (PL 104-113). This law directs federal agencies to focus upon increasing their use of voluntary consensus standards whenever possible to reduce federal procurement and operating costs. The OMB A-119 circular cited earlier in this document was developed to inform government agencies of their statutory obligations in standards-setting activities.
Non-government organizations
In 1996, NIST identified over 600 non-governmental organizations that had or were developing standards. Of these, approximately 500 were actively developing standards.
In general, product-related, non-governmental standards developers can be divided into scientific and professional societies, trade associations, standards-developing organizations, and consortia. In addition, individual companies may develop standards for internal use.
Scientific and professional societies are individual membership organizations that support the practice and advancement of a particular profession — for example, the American Society of Mechanical Engineers (ASME). Several societies, particularly in the engineering disciplines, develop technical standards.
Trade or industry associations are organizations of manufacturers, suppliers, customers, service providers, and other firms active in an industry sector. Many industry associations develop or sponsor the development of standards for the products manufactured by their members, or for products used by their industry. Examples of trade associations that develop product-related standards include the American Petroleum Institute (API) and the Electronic Industries Association (EIA).
Standards-developing organizations (SDO) are membership organizations that are founded specifically to develop standards. They do not limit their membership to an industry or profession, and publishing standards and associated documentation accounts for the majority of their revenue. An example of an SDO is ASTM International.
Consortia are informal groups of standards developers that get together to address the specific concerns of their group. They are mainly used in the high-technology sector where advances outpace the development time of consensus standards, and are mainly involved in interface and interoperability standards. For example, the Open Geospatial Consortium (OGC) develops standards to enable the sharing of geospatial data in geographical information systems (GIS).
ANSI
The American National Standards Institute (ANSI) does not develop standards, but the private, nonprofit membership organization plays several important roles in administering and coordinating the voluntary standards system. ANSI sets guidelines for the development and coordination of voluntary consensus standards, reviews and accredits many U.S. standards-setting organizations against these guidelines, and approves individual standards. Standards approved by ANSI are designated American National Standards. ANSI also represents U.S. positions in international standards activities.
More than 240 private organizations are ANSI-accredited standards developers. More information about the development process is available at https://www.ansi.org/standards_activities/overview/overview?menuid=3.
Voluntary standards development
The two most widely used methods for developing voluntary standards are the committee and canvass methods. Either method may be used to comply with the ANSI accreditation guidelines.
Under the committee method, a committee of interested parties is established to develop and maintain the proposed standard. Membership on the committees may be open to individuals within an organization or to all interested parties. When all parties that have an interest in the outcome of the standard have the opportunity to participate and no single interest dominates, the committee is considered to be “balanced.” The procedures used to develop the standard itself will vary depending upon the organization developing the standards. These procedures typically address requirements for determining when consensus has been reached, due process, appeal of adverse decisions, and consideration of negative votes or comments.
The canvass method is used by organizations to gain acceptance for standards that they have already developed internally. The proposed standard is submitted to balloting by organizations representing a variety of interests. Any returned objections or comments must be addressed and satisfactorily resolved. The changes must then be re-balloted and approved before the standard may be released to the public.
Benefits of standards
The use of standards in the design and manufacture of products can benefit product safety. Conformance to recognized standards might also be helpful in the defense of product liability claims.
Product safety
Conformance to product standards can improve product safety in several ways. The specific benefits will depend upon the type of standard.
The most important benefit is that product standards are an accumulation of the prior design work involving a product. This knowledge can be used to provide designers with basic safe design information so that they do not have to “reinvent the wheel.” It may also alert designers to potential safety problems that they may not have considered.
Use of standardized designs and materials may ensure the compatibility of parts, materials, and processes between product manufacturers. This can reduce the need for specialized testing to ensure that a component meets the expectations of the designer.
Product standards may improve communication between product manufacturers and their component suppliers. Reference to a recognized product standard for a component replaces the need for a manufacturer to specify detailed performance criteria in supply contracts. Also, product standards may promote uniform criteria or methods for evaluating the performance of similar products made by different manufacturers.
Product liability
Compliance with product safety standards may be useful in the defense of product liability claims based upon negligence. The amount of usefulness will depend upon whether the standard is a mandatory or voluntary standard, and on the specific facts of the case. The key issue is whether the standard establishes a recognized duty, or standard of care, for the manufacturer.
A federal statute may impose a duty or standard of care or conduct on a product manufacture and may pre-empt particular state statutes or rules of common law. Evidence of compliance with this standard may free a product manufacturer from product liability. The pre-emptive effect of federal product safety statutes on product liability claims is a fiercely litigated area and there is a substantial body of case law interpreting individual statutes.
Statutes, regulations, or ordinances may define a duty or standard of care without eliminating common-law negligence liability for defective products. Compliance with these mandatory standards may be used as evidence that the manufacturer acted in a non-negligent manner. Conversely, in some jurisdictions, courts may consider evidence of noncompliance with a mandatory standard sufficient to render the manufacturer legally negligent.
In general, compliance with voluntary standards will not have the force of law and will not define a duty or standard of care. Compliance or lack of compliance with a voluntary standard will simply be another fact for the jury to consider when weighting the reasonableness of the manufacturer’s conduct under the circumstance of the case. The adequacy of the voluntary standard will be at issue since such standards will not have the presumption of validity that a mandatory standard would have.
Limitations of standards
There are several important limitations to the use of product standards in product safety management and product liability defense.
Many products are not covered by industry-wide safety standards. Either the products represent proprietary designs or there is not sufficient interest to develop a formal standard.
The standards that are available may be inadequate. There are numerous types of inadequacies. The standard may not address all hazards associated with a product design. The requirements of the standard may be difficult to understand, lack detail, or lack completeness. Standards developed by a consensus process are by nature minimum standards. Also, lack of coordination between multiple standards may result in contradictory requirements.
Standards that are not reviewed and updated in a timely manner may no longer represent the “state of the art” for the product area. Strict compliance with such standards may actually cause the safety of a product to be lessened.
Most importantly, conformance to a standard will not be sufficient to defeat a claim that a product was negligently designed if it can be shown that a reasonable manufacturer would have taken additional precautions. This is to prevent situations where the level of safety is intentionally set low to insulate the standard’s user from liability. Also, compliance with a standard will be irrelevant if the product aspect that caused the injury was not addressed by the standard.
Risk control guidance
The following section provides guidance on using standards for product safety management and product liability prevention. Product manufacturers should identify all mandatory and voluntary safety standards applicable to their product.
Mandatory standards may include state, federal, or international requirements depending upon where the product will be marketed. Product designs should incorporate these requirements and finished products should be tested for conformance to these requirements. Occasionally, a product design may advance the state of the art in product safety beyond mandated requirements and the design improvement may conflict with the mandated requirement. In such cases, the manufacturer should request a formal exemption or waiver from the requirement from the respective authority having jurisdiction. This documentation should be maintained in the product file along with the design technical information and materials to support the request.
Voluntary safety standards should be reviewed by product designers for adequacy. The standards review should be documented in the development file for the product. Manufacturers should consider adequate standards when designing products and reviewing product designs. Manufacturers should conform to voluntary requirements that improve the safety and operability of their product. An evaluation program should be established to assess the conformance of produced products to the design standards. Manufacturers should consider product certification of key safety features. See E&S Product Safety Report PS-30-20, Product Certification, for more information.
Product manufacturers should monitor standards’ activity in areas affecting their products. This review should include new standards under development and standards being reviewed. Manufacturers should consider participating in the development and maintenance of safety standards affecting their products.
Product manufacturers should incorporate standard components, whenever feasible, to reduce the amount of specialized testing and conformity assurance required.
References
- 63 Am Jur 2d, Products Liability, §§ 373 - 406 “Effect of Standards, Legislation, or Regulation on Negligence.” Westlaw (database updated August 2018).
- Breitenberg, M. The ABC’s of Standards-Related Activities in the United States, NISTIR 7614. Gaithersburg, MD: National Institute of Standards and Technology, 2009.
- International Organization for Standardization (ISO) and International Electrotechnical Commission (IEC). ISO/IEC Guide 2: 2004, Standardization and Related Activities – General Vocabulary. Geneva: CH: ISO, 2004.
- National Institute of Standards and Technology (NIST). Standards Activities of Organizations in the United States. NIST Special Pub. 806. Gaithersburg, MD: NIST, 1996.
- National Research Council. Standards, Conformity Assessment, and Trade Into the 21st Century. Washington, DC: National Academy Press, 1995.
- “Resources: Glossary.” StandardsPortal.org, a Resource for Global Trade. https://www.standardsportal.org/usa_en/resources/glossary.aspx. (accessed December 4, 2018).
- Revision of OMB Circular A-119. “Federal Participation in the Development and Use of Voluntary Consensus Standards and in Conformity Assessment Activities.” Office of Management and Budget. (January 27, 2016). https://www.gpo.gov/fdsys/pkg/FR-2016-01-27/pdf/2016-01606.pdf.
To learn more about Hanover Risk Solutions, visit hanoverrisksolutions.com
Copyright © 2018, ISO Services, Inc.
The recommendation(s), advice and contents of this material are provided for informational purposes only and do not purport to address every possible legal obligation, hazard, code violation, loss potential or exception to good practice. The Hanover Insurance Company and its affiliates and subsidiaries ("The Hanover") specifically disclaim any warranty or representation that acceptance of any recommendations or advice contained herein will make any premises, property or operation safe or in compliance with any law or regulation. Under no circumstances should this material or your acceptance of any recommendations or advice contained herein be construed as establishing the existence or availability of any insurance coverage with The Hanover. By providing this information to you, The Hanover does not assume (and specifically disclaims) any duty, undertaking or responsibility to you. The decision to accept or implement any recommendation(s) or advice contained in this material must be made by you.
LC NOV 2018-348
171-1744 (6/19)