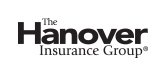
Powered industrial trucks
Material handling is a significant safety concern. During the movement of products and materials, there are numerous opportunities for personal injury and property damage if proper procedures and caution are not used. This applies to all powered industrial trucks, including forklifts, tractors, platform lift trucks, motorized hand trucks, and other specialized industrial trucks powered by electric motors or internal combustion engines. The information in this document and additional applicable OSHA standards found in 29 CFR 1910.178 should be used to understand your responsibilities under the OSHA Powered Industrial Truck Standard.
Responsibilities
Identify the person who will be responsible for developing, implementing, and administering the forklift safety program. This person will review the forklift safety program annually and make recommendations for revisions if necessary and should ensure that all employees who operate or work near forklifts are properly trained.
Pre-qualifications for powered industrial truck operators
All employees who will operate powered industrial trucks (PIT) should meet the following basic requirements prior to starting initial or annual training:
- Have no adverse vision problems that cannot be corrected by glasses or contacts.
- Have no adverse hearing loss that cannot be corrected with hearing aids.
- Have no physical impairments that would impair safe operation of the PIT.
- Is not taking any medication that affects perception, vision or physical abilities.
Inspections
Forklifts – Forklifts should be inspected daily, prior to use, by the authorized operator. If any deficiencies are found the operator should tag out the forklift with a “do not operate” tag and the Forklift not used until the deficiency has been corrected.
Trucks/trailers – All trucks and trailers should be inspected before loading. If any deficiencies are found the truck/trailer should not be loaded until the deficiency has been corrected.
Trailer restraint (dock locks, levelers, wheel chocks) – All safety devices designed to prevent trailer movement should be inspected prior to loading operations to ensure they are properly connected/positioned and working properly.
Training
An experienced operator, selected by the employer, should conduct training for PIT operators. All training and evaluation should be completed before an operator is permitted to use a PIT without continual and close supervision.
Trainees may operate a powered industrial truck only:
- Under the direct supervision of persons, selected by the employer, who have the knowledge, training, and experience to train operators and evaluate their competence; and
- Where such operation does not endanger the trainee or other employees.
Training consists of a combination of formal instruction, practical training (demonstrations performed by the trainer and practical exercises performed by the trainee), and evaluation of the operator’s performance in the workplace.
Initial training
As specified in the OSHA standard, PIT operators should receive initial training in the following truck-related and workplace-related topics:
Truck-related topics:
- Operating instructions, warnings, and precautions for the type of truck the operator will be authorized to operate
- Differences between the truck and automobiles
- Truck controls and instrumentation
- Engine or motor operation
- Steering and maneuvering
- Visibility (including restrictions due to loading)
- Fork and attachment adaptation, operation, and use limitations
- Vehicle capacity
- Vehicle stability
- Vehicle inspection and maintenance that the operator will be required to perform
- Refueling and/or charging and recharging of batteries
- Operating limitations
- Operating instructions, warnings, or precautions listed in the operator’s manual for the types of vehicle that the employee is being trained to operate
Workplace-related topics:
- Surface conditions where the vehicle will be operated
- Composition of loads to be carried and load stability
- Load manipulation, stacking, and unstacking
- Pedestrian traffic in areas where the vehicle will be operated
- Narrow aisles and other restricted places where the vehicle will be operated
- Hazardous (classified) locations where the vehicle will be operated
- Ramps and other sloped surfaces that would affect the vehicles’ stability
- Closed environments and other areas where insufficient ventilation or poor vehicle maintenance could cause a buildup of carbon monoxide or diesel exhaust
- Other unique or potentially hazardous environmental conditions in the workplace that could affect safe operation
Refresher training and evaluation
Refresher training, including an evaluation of the effectiveness of that training, should be conducted every three years to ensure that the operator has the knowledge and skills needed to operate the powered industrial truck safely.
Refresher training in relevant topics should be provided to the operator in the following situations:
- The operator has been observed operating the vehicle in an unsafe manner.
- The operator has been involved in an accident or near-miss incident.
- The operator has received an evaluation that reveals that the operator is not operating the truck safely.
- The operator is assigned to drive a different type of truck.
- A condition in the workplace changes in a manner that could affect safe operation of the truck.
Safe operating procedures
The following procedures should be considered to minimize the potential for incidents. Additional requirements can be found in the OSHA Powered Industrial Truck standard 29 CFR 1910.178.
Forklifts
All employees who will operate powered industrial trucks (PIT) should meet the following basic requirements prior to starting initial or annual training:
- Only authorized and trained personnel should operate PITs.
- All PITs should be equipped with an overhead cage, fire extinguisher, rotating beacon, back-up alarm, and seat belts. The operator should wear seat belts at all times.
- The operator should perform daily pre- and post-trip inspections
- Any safety defects (such as hydraulic fluid leaks; defective brakes, steering, lights, or horn; and/or missing fire extinguisher, lights, seat belt, or back-up alarm) should be reported for immediate repair and the PIT taken out of service until the repair is completed.
- Operators should follow the proper recharging or refueling safety procedures established by the employer.
- Loads should be tilted back and carried no more than six inches from the ground. Loads that restrict the operator’s vision should be transported backwards or use the assistance of a spotter.
- PITs operators should obey posted speed limits and slow down on wet floors and when going around corners.
- PIT operators in high lift areas should wear hard hats. Operators should sound the horn and use extreme caution when meeting pedestrians, making turns, and cornering.
- If PITs are used to raise employees, a manufactured platform (cage with standard rails and toe-boards) should be used and the forklift should be approved by the manufacturer to lift employees.
- Aisles should be maintained free from obstructions, marked, and wide enough (six-foot minimum) for vehicle operation.
- Lift capacity should be marked on all PITs. Operators should assure the load does not exceed rated weight limits.
- When unattended, PITs should be turned off, forks lowered to the ground and the parking brake applied.
- All PITs (with the exception of pallet jacks) should be equipped with a multi-purpose dry chemical fire extinguisher.
- Operators should report all accidents, regardless of fault and severity, to their supervisor.
- Trailers should be parked squarely to the loading area and have wheels chocked in place.
- Only stable or safely arranged loads can be handled. Exercise caution when handling off-center loads that cannot be centered.
Changing and charging storage batteries
- Battery charging installations should be located in areas designated for that purpose.
- Facilities should be provided for flushing and neutralizing spilled electrolyte, for fire protection, for protecting charging apparatus from damage by trucks, and for adequate ventilation for dispersal of fumes from gases.
- When charging batteries, acid should be poured into water. Water should not be poured into acid.
- Trucks should be properly positioned and brake applied before attempting to change or charge batteries.
- Care should be taken to assure that vent caps are functioning. The battery (or compartment) cover(s) should be open to dissipate heat.
- Precautions should be taken to prevent sparks, or electric arcs in battery charging areas.
Loading trucks and trailers
- The flooring and frame of trucks and trailers should be inspected for damage and weakness before driving onto them with forklifts.
- The brakes of trucks should be set and wheel chocks placed under the rear wheels to prevent the trucks from rolling while they are boarded with powered industrial trucks.
Operations
- If at any time a powered industrial truck is found to be in need of repair, defective, or in any way unsafe, the truck should be tagged and taken out of service until it has been restored to a safe operating condition.
- No person should be allowed to stand or pass under the elevated portion of any truck, whether loaded or empty.
- When a powered industrial truck is left unattended, loads should be fully lowered, controls neutralized, power shut off, and brakes set. Wheels should be blocked if the truck is parked on an incline.
- There should be sufficient headroom under overhead installations, lights, pipes and sprinkler systems to prevent contact with the mast or load.
- An overhead guard should be used as protection against falling objects.
Maintenance
- Any power-operated industrial truck not in safe operating condition should be removed from service. Only authorized personnel should make all repairs.
- Repairs to the fuel and ignition systems of industrial trucks that involve fire hazards should be conducted only in locations designated for such repairs.
- Trucks in need of repairs to the electrical system should have the battery disconnected before such repairs.
Related links
- OSHA – The OSHA website contains helpful information that can be used to develop forklift programs, procedures, training and inspections.
To learn more about Hanover Risk Solutions, visit hanoverrisksolutions.com
The recommendation(s), advice and contents of this material are provided for informational purposes only and do not purport to address every possible legal obligation, hazard, code violation, loss potential or exception to good practice. The Hanover Insurance Company and its affiliates and subsidiaries ("The Hanover") specifically disclaim any warranty or representation that acceptance of any recommendations or advice contained herein will make any premises, property or operation safe or in compliance with any law or regulation. Under no circumstances should this material or your acceptance of any recommendations or advice contained herein be construed as establishing the existence or availability of any insurance coverage with The Hanover. By providing this information to you, The Hanover does not assume (and specifically disclaims) any duty, undertaking or responsibility to you. The decision to accept or implement any recommendation(s) or advice contained in this material must be made by you.
LC APR 2019-230
171-0904 (1/14)