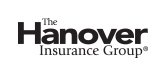
Paper dust in record destruction
Paper is combustible and easily ignitable when finely divided; all that is needed is an ignition source. Under certain conditions, paper dust can create an explosion hazard. In a document destruction operation, both combustible dust and ignition sources are readily available, regardless of whether your operations use fixed equipment, mobile shredding equipment or a combination of both. Without proper controls for this hazard, both your employees and business are at risk.
What can a fire or explosion do to my business?
A fire or explosion will result in damages well beyond the actual physical damage to the truck, building, and/or equipment. Things to consider:
- Possible injuries to people including employees and firefighters that respond to an emergency
- Material not yet shredded end up watersoaked and incapable of being shredded
- Loss of business due to inability to service customers
- Damage to client’s property or simply tarnished reputation from fire in mobile equipment while on client’s premises
What are common ignition sources?
- Sparks generated by metal entering the process such as paper clips, staples, and other metal parts
- Electrical equipment and power supplies
- Plastic contaminants can overheat, melt, and start a fire
- Dust build-up in shredder unit bearings causes lubricants to dry up, resulting in conditions that can cause a spark
- Smoking
- Hot Work
What steps can be taken to minimize this type of loss?
There is no single answer and it depends on your specific situation. It is likely you will need a combination of steps that fall into these categories:
- Management Accountability
- Maintenance
- Housekeeping
- Control of Ignition Sources
- Dust Control System
- Fire Protection
- Employee Training
- Mobile Equipment Considerations
Management accountability
Management should ensure they understand the hazards associated with their particular operations and provide the resources needed to help ensure safe operations for the business. Management should institute the following:
- Develop a prevention and protection scheme tailored to your operations
- Develop and implement written policies for maintenance, ignition control and housekeeping
- Provide employees with proper training
- Implement a policy to encourage the reporting of unsafe conditions or practices
Maintenance
- Maintain shredding equipment in accordance with manufacturers specifications
- Rotate teeth regularly on rotary grinders
- Fire suppression systems on mobile equipment and in building facilities should be inspected and tested in accordance with the National Fire Protection Association (NFPA)
- Implement an Electrical Preventative Maintenance Program
Housekeeping
- Practice good housekeeping—if you can leave a footprint or dust depth is greater than 1/16th of an inch, there is a problem. Dust should be cleaned regularly from building members, equipment, etc.
- Make sure to check and clean hidden areas where combustible dust can accumulate
- Use cleaning methods that do not generate dust clouds, such as low velocity sweeping
Control of ignition sources
- Control mechanical sparks and friction
- Prohibit smoking and use of open flames in areas used for storage or processing of combustible material
- Use appropriate electrical equipment and installation methods in accordance with NFPA 70
- Control static electricity by properly bonding equipment to ground
- Use separator devices, such as a tramp metal separator, to remove foreign materials from process materials
Dust control
- Install dust control system on equipment
- Keep equipment away from dock doors to avoid wind gusts that disrupt dust control patterns
- Minimize the escape of dust from process equipment and ventilation systems
Fire protection
- Provide automatic sprinkler protection in buildings, dust collection systems, ductwork conveying combustible dust that is 10 inches in diameter or larger, and other equipment as needed
- Provide a FM (Factory Mutual) approved automatic spark suppression system in dust collection ductwork
- Provide automatic fire protection on mobile trucks
- Provide an adequate number of listed fire extinguishers in both buildings and on mobile equipment
- Provide explosion venting where needed
Employee training
Employee training should include all of the following and should be completed periodically as a refresher or when there are changes to processes:
- Safe work practices
- Ignition source control, housekeeping practices, and dust control
- Recognition of unsafe conditions and steps to take such as alerting management and taking preventative action
- Location and use of fire extinguishers
- Operation of fire protection systems on mobile shredding equipment or specific fixed equipment
Mobile shredding equipment control
- Empty trucks of shredded material before closing for the night; trucks should NOT be left full of material overnight
- Avoid parking trucks inside the building or on a loading dock, to prevent fire on the truck from spreading to a structure
- Regular maintenance on equipment; check oil lines, belts on motors, cutterheads, etc.
- Provide automatic fire suppression system
- Train operator in fire suppression system if manual, or automatic system with secondary manual activation
OSHA’s role
A dust explosion at the Imperial Sugar facility in 2008 killed 14 people. OSHA responded to this tragedy by re-introducing a National Emphasis Program (NEP) on combustible dust. The NEP is focused on 64 national industries, including those involved in scrap, refuse, and waste materials for paper products. For more information visit OSHA's Combustible Dust page.
Related links
There are various resources available to provide guidance on protecting your facility from the hazards associated with processing paper. Listed below are some references that could be helpful:
- National Fire Protection Association
- NFPA 654, Standard for the prevention of Fire and Dust explosions from the Manufacturing, Processing, and Handling of Combustible Particulate Solids
- NFPA 70, National Electrical Code®
- OSHA
- 29CFR 1910.94-Ventilation Standard
- 29CFR 1910.22(a)(1)-Workplace Cleanliness
- National Association for Information Destruction
- Professional Records & Information Services Management
To learn more about Hanover Risk Solutions, visit hanoverrisksolutions.com
The recommendation(s), advice and contents of this material are provided for informational purposes only and do not purport to address every possible legal obligation, hazard, code violation, loss potential or exception to good practice. The Hanover Insurance Company and its affiliates and subsidiaries ("The Hanover") specifically disclaim any warranty or representation that acceptance of any recommendations or advice contained herein will make any premises, property or operation safe or in compliance with any law or regulation. Under no circumstances should this material or your acceptance of any recommendations or advice contained herein be construed as establishing the existence or availability of any insurance coverage with The Hanover. By providing this information to you, The Hanover does not assume (and specifically disclaims) any duty, undertaking or responsibility to you. The decision to accept or implement any recommendation(s) or advice contained in this material must be made by you.
LC JAN 2019 12-81
171-0972 (01/14)