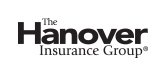
Instruments and controls
Instruments and controls are frequently key components in large, complex systems that affect consumers’ daily lives. This page provides information on the basic classes of instruments and controls, their insurance exposures and loss control methods that may be employed.
Instruments and controls are in common use in homes, places of employment, production facilities and in every form of powered transportation vehicle. They are usually key components in large, complex systems and a malfunction may result in bodily injury, property damage and/or business interruption.
As a result, instruments and controls present an unusually complex series of exposures. This page provides information on the basic classes of instruments and controls, insurance exposures and loss control methods that may be employed.
Classes of devices
An instrument may be defined as a device for determining the value or magnitude of a quantity or a variable. A control is a device for regulating a system or component in manual or automatic operation. An instrument and a control may be incorporated in one device. For example, a thermostat used in a home heating/air-conditioning system measures the temperature in a room and then acts to regulate it by controlling a furnace or air-conditioning unit.
Measurement parameters
Instruments and controls are used to measure and regulate the following parameters:
- Linear or angular displacement
- Velocity
- Acceleration
- Pressure
- Temperature
- Light
- Sound
Many other parameters may be monitored for special applications. For example, the viscosity of fluid, radiation levels, pH, etc.
Power
Instruments and controls may be powered by electrical, pneumatic, or hydraulic systems. The majority of these products are electrically-powered, but many industrial applications require hydraulic or pneumatic systems to eliminate the hazards associated with unintended electrical discharges.
Device categories
Instruments and controls have traditionally been divided into two categories: analog and digital devices. An analog instrument is a device that produces some form of output that is continuously representative of the parameter being monitored. Meters, galvanometers, thermocouples, manometers and strain gages are included in this category. An automotive speedometer is another example of this type of device.
Digital devices employ analog devices to measure parameters and then convert their output to a series of electrical pulses at precise intervals that may be counted by electronic circuitry. Digital devices may be read more accurately than analog meters since the error is reduced to one digit over the entire range of the device. In addition, digital formats may be processed electronically; this is not possible with analog systems. The odometer in an automobile is an example of a digital device.
Devices that are used to convert analog signals to a digital format are called A/D converters. Conversely, devices used to convert digital systems to an analog format are called D/A converters. The majority of these devices are solid state units; chips mounted on printed circuit boards are employed for these functions.
Additional classifications applicable to instrument and control systems are “manual” and “automatic.” A manual system is one where all adjustments to the controlled parameter are performed by the user. For example, if the driver of an automobile wants the vehicle speed to be 50 mph, the accelerator is depressed and the driver checks the speedometer to determine when the accelerator pedal should be released.
In an automatic system the driver would engage the automatic control when the proper speed is attained and the speed would then be stabilized at 50 mph. The automatic control that measures the speed and transmits signals to the throttle is called a “servo.” In an automobile, this type of system is sometimes called a “cruise control” and may be an analog or a digital system.
The majority of industrial process control systems are automatic, and the tolerances on the regulation of the controlled parameters are critical. Additional information on this subject is provided in the “Design” section of this report.
Product exposure information
Instruments and controls may present an unusually complex series of exposures. The hazards that contribute to these exposures may be subtle or highly technical. Therefore, it is essential to obtain some preliminary information about the products prior to evaluating the insured’s loss control program. The following are key issues to be considered.
Description
Is the product a single component or a system consisting of a number of components and auxiliary devices? A system will inherently be more complex than a single component. So far, this report has emphasized basic instruments and controls, but a typical “automatic” system may include an amplifier, servo components, and a computer-type controller; each of these devices will contribute to the overall exposure. When the system is used in conjunction with a computer, software may also be included with the system.
Function
Which parameters is the product intended to monitor or control? Is the substance hazardous or toxic? These are some factors that should be considered.
Consequences of failure
What are the consequences of failure of the product? Would this possibility cause bodily injury, property damage, business interruption, or environmental pollution? Could the consequence be catastrophic in magnitude? A defective home temperature gauge would probably produce losses of only slight magnitude. By contrast, a defective control system could produce defective material, cause a production interruption, or possibly an explosion. Therefore it is essential to obtain information concerning where and how the product may be used.
Losses
How many losses/claims/lawsuits have been incurred over a specific period of time? What was the extent of the losses? What corrective measures were implemented to prevent future losses of this type? How many products of this general type are still in the market?
Recalls
How many products were recalled? What were the reasons for the recalls and how were the product defects corrected? Were any governmental agencies involved in the recall?
Manufacturing
What percentage of the parts used in the end-item are obtained from outside sources? Are any of the parts imported?
Repairs/calibration
When an instrument or control is in need of repairs, where is the work performed? Is the product capable of being recalibrated by the user or should it be returned for servicing? Or, are there service centers established to perform this work? This information should be clearly included in instructions given to the customer.
Exports
Are any of the products intended for export? Do the products conform to the standards established by the host country?
Marketing
Are other companies involved in the marketing and sales of the product? If other organizations are involved, how are their salespersons supervised? Has diversity in language been considered in sales and instructional literature?
Dormant controls
Does the product contain a device that only reacts in case of an emergency? For example, the brake fluid level warning light on an automotive dashboard may malfunction if the bulb is burned out. The condition of the device is checked when the engine is started and the control flashes to indicate that it is functional. However, some dormant controls are not provided with this type of checking feature and may be inoperative without providing a warning.
Product loss control program
The loss control programs for instruments and controls have certain similarities but important differences. Both products are precision devices and may be key components in larger systems. However, instruments are passive devices; they have a negligible effect on the parameters that they monitor. Conversely, controls have a major effect on the parameters that they monitor. The automotive speedometer and cruise-control, previously noted, exemplify this basic difference. When a control system used in an industrial system application fails, the result may include bodily injury, property damage, production of defective material, and business interruption. The loss control program should reflect the special requirements of instruments and controls.
The elements of the program should include:
- Design
- Standards
- Testing
- Quality control
- Communication with customers
Design
The following section provides information on important considerations for the design of instruments and controls.
InstrumentsInstruments normally consist of two elements: a sensor that is connected to, or near, the parameter to be monitored and the read-out device or dial that provides a visual indication of the information being supplied by the sensor. The most important considerations in the design of instruments include:
- Parameters to be monitored
- Environmental conditions
- Power requirements
- Accuracy
- Display
Parameters may be gases, liquids or solids. The characteristics to be measured may include any of the fundamental parameters listed earlier in this report, or other items, such as viscosity, ph, radiation, electromagnetic fields or other physical or chemical data.
The environmental conditions under which the instrument should function are a vital engineering consideration. The environment may be relatively “safe,” moderately dangerous, or very dangerous. Special materials or seals may be needed so that the instrument can survive the ambient conditions and function in a reliable manner.
Instruments may be powered by AC or DC electrical power, with various voltages and frequencies; gas; or hydraulic power. The accuracy of the instrument, and the definition of how it is to be measured, are also important considerations.
The type of read-out, whether analog or digital, should be determined.
ControlsIndustrial control systems are usually made up of a complex array of components; failure of any one of the components could result in serious losses. Therefore, the design of controls used for industrial applications is a relatively complex engineering process that should be carefully scrutinized.
The considerations for instruments outlined above are also applicable to controls. In addition, the following should be considered:
- System accuracy
- Compatibility
- Power
- Failure consequences
The overall accuracy of the control system, including inherent errors in all components, should be determined, as well as compatibility with other systems that may be controlling characteristics in the same media.
Some control systems may not function properly when energized by conventional sources of power. They may require a dedicated power supply or an auxiliary power supply. When the source of power is a compressed gas system, the gas should be exceptionally clean and free of grit and oil. The tolerances required on power supplies are another important consideration.
The consequences of failure of a control system should be analyzed and emergency procedures designed into the system. Some control systems are designed to be “fail-safe” (i.e., if the system fails the controlled parameters are returned to a neutral or “safe” condition). Or, a “redundant” or spare system may be provided that functions when the primary system becomes defective. This procedure is used in some types of control systems found in aircraft, space vehicles, and critical industrial processes.
Standards
Instruments and controls should conform to applicable codes and standards. Standards for instruments and controls are grouped into two broad categories:
- Proprietary standards developed by manufacturers or trade groups for special purpose products.
- Standards developed by consensus organizations that cover products used for a broad range of applications.
Proprietary type standards are written to address the need to codify the engineering characteristics of a line of products. These standards are essential to customers who purchase instruments and controls. The standards are usually written to outline the tests performed on products and the tolerances applicable to performance specifications. Verification by an independent testing organization is important.
Testing
The testing phase of a product development program should clearly document that the end-item is in conformance with published specifications for the product. Test data should be derived from prototypes of the product, as well as samples derived from production. The tests should include data on each item listed in sales data sheets, as well as each item in applicable standards. All data should be dated and witnessed by an appropriate laboratory supervisor. Information should also be recorded on the test equipment used to obtain the data and when each piece of equipment was calibrated.
Independent verification of test results by a recognized third-party testing laboratory is important in case of litigation. The laboratory should be an organization certified to perform this work.
Quality control
Instruments and controls are key components in systems; consequently, quality control of each product is a vital part of the product loss control program. Basic quality control consists of careful monitoring of all purchased materials and services, production, and the packaging of products. However, in a practical sense, quality control for “precision” products is still an art that emphasizes proprietary processes not found in published standards. Fortunately, modern analysis of quality control practices is based on an evaluation of the managerial organization of the manufacturer; these criteria have been developed over a period of decades and have been codified in a number of American National Standards Institute (ANSI) and American Society for Quality (ASQ) documents.
Communication
Many instruments and controls are sold in retail stores as “over-the-counter” items. Little instruction is needed to successfully install and use these products. However, even these mundane products should be sold with basic instructions for use, and warnings should be provided concerning foreseeable hazards associated with them. These include such items as thermostats, pressure relief valves, plumbing equipment, and electrical hardware.
Instruments and controls used in industrial products and processes are fundamentally in a different category. Performance characteristics, environmental conditions, and dynamic response are critical concerns. Therefore, communication between the user and the manufacturer is an important consideration. The performance of the system should be clearly established in a written document after appropriate discussions between the user and the manufacturer. Some of these considerations include:
- Details on performance
- Procedures for amending the original performance specifications
- Delivery schedules
- Test methods to be used
- Test equipment to be used
- Printed instructions to be supplied
- Servicing to be provided by the manufacturer
- Shipping methods to be employed
Disputes on any of the above items could result in litigation and expensive settlements.
References
- Engineering and Safety Service. Product Certification. PS-30-20. New York, NY: AISG, 1993.
- —. Survey Guidelines. PS-30-50. New York, NY: AISG, 1993.
- —. The ISO 9000 Standards. PS-30-11. New York, NY: AISG, 1999.
- Baumeister, P. and Avallone, E. Marks Standard Handbook for Mechanical Engineers. New York, NY: McGraw-Hill, 1978.
- Considine, D. Process/Industrial Instrument Control Handbook. New York, NY: McGraw-Hill, 1993.
- “Instruments and Controls” in Kirk-Othmer Encyclopedia of Chemical Technology, 4th ed. New York, NY: Wiley, 1981.
To learn more about Hanover Risk Solutions, visit hanoverrisksolutions.com
Copyright ©2002, ISO Services Properties, Inc.
The recommendation(s), advice and contents of this material are provided for informational purposes only and do not purport to address every possible legal obligation, hazard, code violation, loss potential or exception to good practice. The Hanover Insurance Company and its affiliates and subsidiaries ("The Hanover") specifically disclaim any warranty or representation that acceptance of any recommendations or advice contained herein will make any premises, property or operation safe or in compliance with any law or regulation. Under no circumstances should this material or your acceptance of any recommendations or advice contained herein be construed as establishing the existence or availability of any insurance coverage with The Hanover. By providing this information to you, The Hanover does not assume (and specifically disclaims) any duty, undertaking or responsibility to you. The decision to accept or implement any recommendation(s) or advice contained in this material must be made by you.
LC MAR 2019 11-122
171-0901 (2/14)