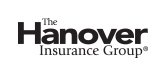
Hydraulic fluids
Hydraulic fluids can present a serious fire hazard due to their combustibility and the high operating pressures of most hydraulic systems. This report discusses the different types of hydraulic fluids; the hazards involved, and recommended loss control measures.
Hydraulic systems use pressurized liquid, for example, oil or water, to produce thousands of pounds of pressure and transmit that pressure into force at a distant location. Industrial plants use hydraulic fluid in a wide variety of devices to transmit pressures through a closed system. Hydraulic fluid systems provide the ability to substantially multiply force, respond quickly, and have the flexibility to be adapted for many uses and applications. Hydraulic fluids are also widely used in the automobile industry for actuating both power steering and power brake systems of vehicles.
Conventional hydraulic fluids are petroleum oils that are used to transfer energy in various types of machinery. When this fluid under pressure escapes through an opening, such as a ruptured hose, gasket, or pipe joint, it can become atomized. When exposed to a heat source, this atomized fluid may ignite and lead to a rapidly developing fire. Hydraulic fluids can form dangerous mists or sprays from small leaks at pressures as low as 250 psi (1,724 kPa). The size of the droplets and their dispersion in the air will affect the degree of fire hazard. Instances of sprays reaching 40 ft. (12 m) from the point of origin have been reported. When ignited, this spray can become a torch, often with devastating results, including the loss of property and life. See the Fatality Assessment and Control Evaluation (FACE) Report “Shipyard Welder Ignites Hydraulic Fluid and Is Fatally Burned” for one example.
Even though some of the “newer” hydraulic fluids are considered less hazardous, they can still ignite under certain conditions. If a less-hazardous substitute for a petroleum-based fluid is being considered, only those that have been tested and listed (or approved) by a nationally recognized testing laboratory should be used. Hydraulic fluids present a serious fire hazard due to their combustibility and the high operating pressures of most hydraulic systems. This report discusses the different types of hydraulic fluids, the hazards involved, and recommended loss control measures.
Types of hydraulic fluids
Commercially available hydraulic fluids are generally listed in five basic categories:
- petroleum-based oils
- high-water-content emulsions
- water-in-oil emulsions
- water-glycol fluids
- synthetic fluids
The terms “fire-resistant” and “less hazardous” are used interchangeably to describe products that have higher flash points than the petroleum-based oils.
Petroleum-based
From a performance standpoint, petroleum-based hydraulic fluids are the most desirable fluids. This is due to their ability to lubricate efficiently while not corroding machinery and seals. Petroleum-based hydraulic fluids are readily available in a wide range of viscosities and are relatively inexpensive.
The main problem with the petroleum-based hydraulic fluids is their combustibility. Flash points for these fluids range between 300°F (149°C) and 600°F (315°C). Even though the flash point is relatively high in comparison to flammable liquids, when the oil is discharged under pressure in a mist form, it ignites easily and burns rapidly.
High-water-content emulsions
High-water-content emulsions are less hazardous than petroleum-based hydraulic fluids. These fluids are formulations that contain high percentages of water, typically greater than 80 percent. Due to the high concentration of water present, operating temperatures of these hydraulic fluids must be maintained between 32°F (0°C) to prevent freezing, and below 140°F (60°C) to prevent evaporation, in open storage reservoirs. Most of the high-water-content emulsions available have a tendency to corrode aluminum alloys and other soft-metal alloys.
Water-in-oil emulsions
Water-in-oil emulsions are less hazardous than petroleum-based hydraulic fluids. These fluids are formulations consisting of petroleum oil, water emulsifiers, and selected additives. The water-in-oil emulsion consists of oil surrounding finely divided water droplets that are uniformly dispersed throughout the mixture. This inverted emulsion ensures that only the oil, not the water, contacts and lubricates the moving parts.
If the water-in-oil emulsion is exposed to a source of ignition, the water breaks out of the emulsion to cool and blanket the combustible material. Maintaining the appropriate water content in this type of liquid is very important.
As the water evaporates, the viscosity of the fluid decreases. Increasing the water content thickens the emulsion, increases the viscosity, and maintains the liquid’s fire-resistant properties.
Water-glycol fluids
These solutions, consisting of water, glycols, thickeners, and other additives, are formulated to create a hydraulic fluid with the necessary properties, such as viscosity, for satisfactory use in hydraulic systems. The water-glycol fluids are less hazardous than petroleum-based hydraulic fluids.
Synthetic fluids
Synthetic fluids were designed to replace petroleum oils in hydraulic applications where the operating conditions preclude the use of combustible products. They are non-water-containing fluids, such as phosphate esters or blends of phosphate esters with petroleum oils. Often referred to as fire-resistant hydraulic fluids, synthetic fluids are popular in the aviation, defense, and electronics industries. Water-glycol and water-in-oil emulsion hydraulic fluids are not compatible with synthetic fluids; therefore, systems must be thoroughly drained and flushed before changing from one type of fluid to another.
Risk control measures
The severity of the hazard is dependent on the number of hydraulic machines and their fluid capacities. These factors, however, cannot be easily controlled during accidental escape of pressurized hydraulic fluid. Some primary methods of exposure control are apparent: removing all possible sources of ignition from the areas of exposure, using a less-hazardous hydraulic fluid, shutting off the flow of hydraulic fluids immediately, and providing automatic sprinkler protection. [1]
Fire suppression and alarm systems
In buildings where hydraulic systems are installed, fire alarm systems should be designed, installed, maintained, and monitored in accordance with requirements of NFPA 72, National Fire Alarm Code, published by the National Fire Protection Association (NFPA). The fire alarm system should be covered by a service and maintenance contract, and regularly tested and inspected.
An automatic fire sprinkler system should be installed in accordance with requirements of NFPA 13, Standard for the Installation of Sprinkler Systems. Requirements for maintaining sprinkler systems are provided in NFPA 25, Standard for the Inspection, Testing, and Maintenance of Water-Based Fire Protection Systems. Sign in to Hanover Risk Solutions' partners page and scroll down to E&S, then go to Risk Management information to search for Fire Protection Report FP-22-06, Sprinklers and Their Applications, for additional information.
Fire extinguishers should be located throughout the facility, in compliance with local codes and as required by NFPA 10, Standard for Portable Fire Extinguishers. Employees should be trained in the care and use of the extinguishers, including proper selection and application for the classes of fire presented.
Operations and maintenance [1][4]
Due to the high pressures at which they operate, hydraulic systems should be checked on a regular basis and worn or damaged parts should be replaced before they fail. Pressure leaks can be caused by the failure of hoses, gaskets, seals, valves, couplings, and unions. These parts, as well as all moving parts, should be checked so that vibration does not loosen couplings or other fittings.
The principal cause of breakage or leakage of hydraulic lines is excessive vibration. Isolation of sources of mechanical vibration by means of flexible hoses or swivel joints should be provided. Leakage at joints may be the result of one or more of the following:
- Unsuitable or inferior joints
- Poor workmanship in preparing the joint
- Faulty installation
- Unusual system characteristics that cause excessive peak surge pressures
Fluids
Hydraulic systems require careful cleaning and preparation before changing from a petroleum-based fluid to a less-hazardous fluid. The system should be carefully drained and a cleaning fluid circulated for at least one day to displace old oil. In addition, special components, such as seals, hoses, and paints, should be evaluated to ensure compatibility with the replacement fluid.
When different fluids are used in the same facility, the fluid for each piece of equipment should be positively identified by a mark on the fill pipe. Mixing of fluid types within a hydraulic system should be avoided.
Other factors to be considered include:
- Check the hydraulic fluid frequently to detect any thermal breakdown or contamination of the materials.
- Provide suitable controls for the equipment. Remote control (in the operator’s path of escape) should be available for shutting down oil pumps or shutting off the flow from the accumulators in case of a leak.
- Provide a schedule of frequent and competent inspections and maintenance on all components of the hydraulic system. Detect leaks immediately and make necessary repairs.
- Use a less-hazardous or fire-resistant hydraulic fluid in all areas where it is not possible to remove the source(s) of ignition.
- Keep all hydraulically-operated equipment and surrounding areas clean and free from fluid residue.
Damage protection
Hydraulic systems, including pumps, hoses, and cylinders, should be protected from damage by physical location, guards, or other barriers. Hydraulic hoses and pipes should be rigidly supported to protect against damage caused by vibration. The entire hydraulic system, including piping, fittings, and gaskets, should be adequate for the pressure(s) involved.
References
- Factory Mutual Engineering Corp. “Hydraulic Fluids.” Property Loss Prevention Data Sheet 7-98. Norwood, MA: FM Global, 2018.
- International Codes Council (ICC). International Fire Code. 2018 ed. Falls Church, VA: ICC, 2018.
- Liming Yuan, Ignition of Hydraulic Fluid Sprays by Open Flames and Hot Surfaces. Pittsburgh Research Laboratory, National Institute for Occupational Safety and Health (NIOSH). Pittsburgh, PA: NIOSH, 2006.
- National Fire Protection Association (NFPA) Fire Protection Handbook. 20th ed. Quincy, MA: NFPA, 2008.
- —. Standard for the Installation of Sprinkler Systems. NFPA 13. Quincy, MA: NFPA, 2019.
- —. Uniform Fire Code. NFPA 1. Quincy, MA: NFPA, 2018.
Copyright ©2019, ISO Services Properties, Inc.
To learn more about Hanover Risk Solutions, visit hanoverrisksolutions.com
The recommendation(s), advice and contents of this material are provided for informational purposes only and do not purport to address every possible legal obligation, hazard, code violation, loss potential or exception to good practice. The Hanover Insurance Company and its affiliates and subsidiaries ("The Hanover") specifically disclaim any warranty or representation that acceptance of any recommendations or advice contained herein will make any premises, property or operation safe or in compliance with any law or regulation. Under no circumstances should this material or your acceptance of any recommendations or advice contained herein be construed as establishing the existence or availability of any insurance coverage with The Hanover. By providing this information to you, The Hanover does not assume (and specifically disclaims) any duty, undertaking or responsibility to you. The decision to accept or implement any recommendation(s) or advice contained in this material must be made by you.
LC MAR 2019-343
171-1742 (6/19)