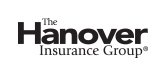
Dust explosions
A dust explosion is the uncontrolled burning of a finely divided combustible material, suspended in air or other gaseous oxidizer. The rapid propagation of combustion and a correspondingly large generation of heat characterize dust explosions. This page provides an overview on the hazards of dust explosions, the materials commonly involved in dust explosions, and the general methods for reducing the risk of explosion. Dust properties influencing the degree of hazard are also discussed.
For a dust explosion to take place, the dust and the atmosphere in which it is suspended must have the following characteristics:
- The dust must be combustible.
- The oxygen content of the atmosphere in which the dust is dispersed must be sufficient to sustain combustion.
- The dust concentration must be above the minimum explosive concentration.
- The particle-size distribution must be capable of supporting combustion.
- There must be an ignition source of sufficient energy to initiate the explosion.
The principal hazard of a dust explosion is the increase in pressure that develops from the expansion of gases from the rapid combustion process. If confined, this pressure can rupture equipment or cause structures to collapse. The amount of damage that will result from a dust explosion varies based on the degree of confinement, and the type, size, and amount of dust involved.
NFPA 69, Standard on Explosion Prevention Systems, published by the National Fire Protection Association (NFPA), defines a combustible dust as "A finely divided combustible particulate solid that presents a flash fire hazard or explosion hazard when suspended in air or the process-specific oxidizing medium over a range of concentrations.” The standard further defines a combustible particulate solid as “An oxidizable, solid-phase material comprising distinct particles or pieces.”
Historically, finely divided combustible solid material, 420 microns or less in diameter (i.e., materials passing through a U.S. No. 40 standard sieve), has been treated as combustible dust, except when testing proved otherwise. However, as noted by the NFPA definitions, size is not always a limiting factor when examining the explosion potential of dusts and particulate matter. Current recommendations in the Annex of NFPA 654, Standard for the Prevention of Fire and Dust Explosions from the Manufacturing, Processing, and Handling of Combustible Particulate Solids, notes that “for consistency with other standards, 500 µm (capable of passing through a U.S. No. 35 standard sieve) is now considered an appropriate size criterion.” However, the annex also notes that fibers, and elongated type materials, that normally will not fit through a U.S. No. 35 standard sieve can still pose an explosion hazard (see the section on “Non-Traditional Dust Explosion Hazards” that follows). Typical materials that can give rise to dust explosions include wheat, flour, sugar, charcoal, aluminum flakes, and paper.
Numerous industries handle combustible dusts at some stage of production. Industries with the greatest exposure are those processing chemicals, pharmaceuticals, plastics, resins, dyes, pigments, agricultural products, coal, foodstuffs, metals and wood or paper products. Plant equipment likely to become involved in explosions include silos, bunkers, dust collection systems, conveying systems, dryers, furnaces, mixers, grinders, polishers and sieves/classifiers. Additionally, some chemical groups, such as organic peroxides and nitro compounds, are particularly associated with explosive behavior.
This report provides an overview on the hazards of dust explosions, the materials commonly involved in dust explosions, and the general methods of loss control. Dust properties influencing the degree of hazard are also discussed.
Loss experience
A dust explosion typically lasts from one to a few seconds after ignition, and it occurs within a confined volume. Because explosions occur so rapidly, investigation information tends to focus solely on post-blast observations. Fortunately, research scientists worldwide have extensively studied and documented the evolution of dust explosions.
A study by Factory Mutual (FM) and its subsidiaries during the period 1983 through 2006 provides some insight into the loss trends of dust-related explosions. During that period, there were 166 dust explosions, which resulted in $284 million in property loss (adjusted to 2007 dollars). Of the 166 incidents, woodworking industries experienced the greatest number of losses (38.5%), followed by food processing (15.6%), and metal processing (10.8%). Collectively, these three industries account for 65% of the incidents, with the remaining 35% of dust explosions spread out among nine other industries.
Since that time, a study conducted by the United States Chemical Safety & Hazard Investigation Board of dust explosion found that from 1980 through 2010, there were more than 356 dust-related fires and explosions, which indicates that the frequency and severity of these dust-related incidents has not decreased.
Loss history clearly shows that dust collectors are by far the leading piece of equipment to experience explosions, accounting for nearly 40% of the incidents. There may be several reasons for this. First, a dust collector deals with dust that is constantly suspended in air. Second, because these systems are designed to handle materials produced elsewhere, the ignition source may be remote from the dust collector. A remote ignition source from a production area can ignite an explosion in the dust collector.
An explosion in impact equipment (i.e., grinders, sanders, pulverizers, hammer mills, chippers, shredders, etc.) is the second most common (13.2%) type of equipment involved. This type of equipment not only creates the dust, but also may produce sufficient heat energy (e.g., spark) to ignite the dust cloud produced.
Hazard overview
The explosion hazard of a combustible dust is like the explosion hazard of a flammable liquid vapor or flammable gas (i.e., an ignitable mixture must be present before an explosion can occur). Similarly, the dust must be placed into suspension (i.e., made airborne) by some mechanism before an explosion can occur. Dust explosions are essentially rapid oxidations; they depend on the composition of the particles and their reactivity to the environment in which they are located.
One unique property of dust explosions is the stacked effect or multiple explosions that typically occur. A small initial explosion occurs, liberating dust from surrounding surfaces (i.e., beams and ledges) and causing them to be placed into suspension in the air. A larger, secondary explosion is propagated through the resultant dust cloud, with ignition supplied by the primary explosion. Often subsequent smaller explosions occur as residual dust is again suspended in air. The danger of these third and fourth explosions is the impact they have on an already weakened structure from the earlier explosions.
Ignition sources
There are hundreds of potential ignition sources, with various temperatures, energies, and durations. Ignition sources for dust explosions include open flames, sparks from equipment, welding, smoking materials, and static. One ignition source that is often overlooked is electrostatic discharge. Electrostatic discharge presents a significant ignition source for flammable liquids, gases and some dusts, and as such, the proper control of the buildup of electrostatic charges is required.
For information on the hazards of electrostatic discharge, see, Fire Protection–Static Electricity on our Risk Solutions Electrical Safety page.
Ignition and explosion severity factors
The hazard of any given dust is related to its ignition sensitivity and explosion severity. Ignition sensitivity is the ease at which a combustible dust can be ignited. Explosion severity describes the violence of the ensuing explosion.
Ignition sensitivity is characterized by two properties: minimum ignition temperature and minimum ignition energy. Minimum ignition temperature is the lowest temperature at which a dust will spontaneously ignite. Minimum energy of ignition is the amount of energy that is required to initiate the most easily ignitable dust mixture.
Explosion severity is also characterized by two properties: maximum rate of pressure rise and maximum explosion pressure. The maximum rate of pressure rise is the rate of change of explosion pressure under optimal conditions. The maximum explosion pressure is the largest pressure generated by a dust explosion.
It is important to recognize that, while each of these conditions can be evaluated individually, the cumulative effect of the conditions will determine the degree of explosion hazard. Some of the factors that affect ignition sensitivity and explosion severity include the ignitable mixture, particle size and shape, moisture, and turbulence.
Ignitable mixture
Often referred to as the “oxygen content of the gas phase,” the ignitable mixture of dust in air is a critical component of a dust explosion. For a dust explosion to occur, there must be sufficient oxygen available in the gas phase to support combustion. Variations in oxygen concentrations affect the ease of ignition and the explosion severity.
Like gas/air mixtures, dust clouds are explosive only within a certain concentration range, which is limited by a lower and upper explosive limit. The lower explosive limit (LEL) is the minimum concentration of combustible dust in the suspending medium (usually air) that will propagate a flame. The upper explosive limit (UEL) is the maximum concentration of combustible dust in the suspending medium (usually air) that will propagate a flame.
As with flammables, the introduction of oxidizers and organic peroxides will significantly enhance the ability of a dust to enter its explosive range. Explosion severity is also a function of concentration. At lower concentrations, less heat is developed, and smaller peak pressures are developed. At higher concentrations, the unburned dust absorbs heat, reducing the intensity.
Particle size and surface area
Particle size strongly influences both ease of ignition and explosion severity. As with any combustion process, the greater the surface area of the fuel, the more readily it will absorb heat. Fuels that also possess less mass per unit of surface area will absorb heat and rapidly form ignitable mixtures. Thus, the finer the dust, the more easily it can be ignited and the greater the explosion severity. As particle size decreases, the ignition temperature, explosion concentration, and energy necessary for ignition decrease and the rate of explosion pressure change increases.
Moisture content
The moisture content of the dust is a significant factor because evaporation of water can take up some of the heat of reaction and prevent an explosion from proceeding so rapidly. A dry dust is often less cohesive and more likely to form an ignitable cloud. As moisture content increases, the resulting explosive force will decrease. This occurs due to the increased energy needs to move the additional weight of the dust. Moisture will affect a particle's resistivity. Additionally, the likelihood of developing static charge that can act as an ignition source decreases, as the moisture content of a material increases.
Turbulence
Turbulence strongly affects ignitibility and explosion severity of dust. When air currents exist that create a disruption (turbulence) in a dust cloud, they tend to disrupt the delicate air-fuel mixture of the dust. By constantly changing the airflow, the dust tends to be pushed away from the LEL and moved toward the higher end of the explosive range. There are, however, cases where the opposite can occur, such as when a fresh air current is introduced into a “rich” dust mixture; this can result in a lowering of the fuel-air mixture in the explosive range.
Turbulence also provides a disruptive force for flame prorogation. As the dust ignition takes place, the combustion reaction turbulence can separate the flame front and direct it toward lesser concentrations, resulting in a larger combustion area, with less focused force. The presence of turbulence, typically, reduces the overall severity of an explosion. However, turbulence alone will not eliminate the potential for an explosion.
Additional factors that can affect the sensitivity and severity of a dust explosion include electrical resistance, presence of impurities, and the shape of the dust.
Non-traditional dust explosion hazards
Dust from non-traditional sources, such as nanomaterial manufacturing, certain flocculent material, and gas/dust mixture processing, may explode more readily than dust from more common dust explosion hazard, according to a study published on-line in Industrial & Engineering Chemistry Research, a journal from the American Chemical Society (ACS). The February 2012 article “Review of the Explosibility of Non-traditional Dusts” states that the energy needed to ignite metal nanomaterials is about 1/30th the energy needed to ignite sugar dust, which was the cause of the 2008 Imperial Sugar disaster in Georgia that killed 14 workers, according to an ACS press release.
The expected increase in ignition sensitivity of nanomaterials as compared to micrometer-sized materials is related to the much larger surface area of nanoparticles than micrometer-sized particles contained in the same given mass of material. Increased surface area presents more atoms that can react with the environment around them. As a result, materials traditionally considered non-explosive could be capable of propagating an explosion when they are present as nanomaterials. However, in many cases, the explosion force begins to decrease as the particle reaches nano size. This differs from general explosive properties that dictate the smaller the particle the greater the ignition sensitivity and explosive force. This decrease is thought to occur because nanomaterials tend to “clump together” or agglomerate, which could make dispersion in air and formation of an ignitable fuel-gas mixture more difficult.
The unique nature of some flocculent materials, such as cottons and polyesters, affects their potential for dust-related explosions. Because flocculent materials are non-spherical and tend to be more elongated or irregular in shape, they do not readily pass through a US No. 40 standard sieve, which is one of the primary methods of classifying a material as a dust. Despite its failure to meet the definition of a dust, flocculent materials should be considered as explosive dusts, since they are combustible and, with limited research available, have been shown to be capable of propagating an explosion. Like nanomaterials, flocculent materials have a high surface area-to-mass ratio, which provides for low ignition sensitivity.
Additionally, there is a growing concern related to the hazards of dust/gas (i.e., hybrid) mixtures as they relate to explosive properties. Hybrid mixtures are a combination of a combustible dust, below its minimum explosive concentration (MEC), and a flammable gas or solvent vapor, below its lower flammable limit (LFL). Individually, neither of these materials (dust or vapor) would be capable of propagating an explosion below their MEC or LEL. However, data suggests that when combined, the hybrid mixture can produce an explosion.
See “Review of the Explosibility of Nontraditional Dusts” on the ACS website at http://pubs.acs.org/stoken/presspac/presspac/full/10.1021/ie201614b for additional information.
Loss control measures
Loss control measures to prevent dust explosions can be divided into two categories: prevention of combustion and mitigation (e.g., limitation of damage). Preventive measures are those that act to remove the conditions necessary for combustion to initiate. Mitigation measures are those that act after the combustion has been initiated and are used to lessen the impact of the explosion. When used in conjunction with each other, these methods can substantially reduce the likelihood and consequences of a dust explosion.
Prevention
NFPA 69 provides two control measures to address explosion prevention. They are oxidant concentration reduction and combustible concentration reduction. However, no discussion on explosion and fire prevention can be complete without addressing the control of ignition sources. Due to the large number of potential sources, control of ignition alone is not an adequate safeguard and such control should be coupled with either oxidant concentration reduction, combustible concentration reduction, or both.
Controlling ignition sources
Separating ignition sources from areas where explosive atmospheres may form will reduce the risk of explosion considerably. The methods used will vary depending on the source of ignition. As with any other combustion process, heated surfaces, sparks, electrical arcs and static discharges should be eliminated. Regular inspection, testing and maintenance of equipment are vital to their proper operation and the prevention of fires.
Electrical systems in a dust environment should be evaluated using NFPA 499, Recommended Practice for the Classification of Combustible Dusts and of Hazardous (Classified) Locations for Electrical Installations in Chemical Process Areas. NFPA 499 “provides information on the classification of combustible dusts and of hazardous (classified) locations for electrical installations in chemical process areas and other areas where combustible dusts are produced or handled.” The area should be provided with electrical equipment and wiring meeting the appropriate class identified and installed in accordance with NFPA 70, National Electrical Code.
Procedures for controlling workplace ignition sources, such as smoking, welding and cutting, should be addressed in a formal fire prevention plan. Welding and cutting operations should comply with NFPA 51B, Standard for Fire Prevention During Welding, Cutting and Other Hot Work. Ideally, such operations should be performed in areas separated from other operations by firewalls and fire doors. Equipment, including torches and fuel/gas cylinders, should be regularly inspected and serviced, and provided with the proper safety mechanisms. Cutting, welding and soldering operations should use a hot-work permitting system.
See E&S Client Handout CH-25-18, Welding and Cutting – Hot-Work Permit, through our Hanover Risk Solutions Partners page for additional information.
Systems that detect and extinguish sparks or embers may be used to augment ignition control programs. Such systems operate by means of detectors that sense the radiation of a hot or glowing particle and actuate a special extinguishing system that quenches the particle.
Combustible concentration reduction
The primary methods of reducing combustible dust concentrations are process modification, use of dust-control equipment, and good housekeeping. Ideally, dust concentrations should be reduced to less than 25 percent of their LFL. While blending of combustible dust with a non-combustible dust material, such as talc or lime, can be used to reduce the concentration of the combustible dust, in most situations, this may cause unacceptable product contamination.
Dust generation can be reduced by processing materials in a wet state (slurry or suspension) or by using granules or coarser particles. Limiting the size of process vessels may be another way of reducing the amount of suspended dust in an operation. In some cases, substitution of non-combustible materials may also be possible. Limiting the number of changes in direction can reduce dust generation during materials transport. Dusty material should be introduced to conveyors via choke feed. Spiral or enclosed conveyors should be used to prevent the escape of dust. Maintenance of such equipment is critical for proper operation.
Dust extraction and control systems should be used to prevent or reduce the concentration of dust clouds within the processing operation and to prevent the escape of dust. NFPA 91, Standard for the Installation of Exhaust Systems for Air Conveying of Materials, should be consulted for recommendations on system design and operation. In operations, such as grinding, buffing and sanding, or other operations where multiple types of dust may be created, dust collection systems should be cleaned after each use. Cleaning will prevent any potential hazards that may be associated with mixing different types of dusts.
Good housekeeping should be practiced as a means of reducing the hazard in areas where the potential for a dust explosion exists. Plant surfaces should be regularly cleaned to prevent the accumulation of dust. Dust layers as small as 1/32-in (0.8-mm) thick can be sufficient to produce uniform dust clouds within the explosive range of most dusts. Vacuum cleaning is generally preferable to brushing or blowing the dust from horizontal surfaces. To facilitate cleaning and minimize dust accumulation, interior surfaces should be made as smooth as possible and window ledges, girders, beams, and other horizontal surfaces designed to minimize deposition of dust. Special consideration should be given to dust that adheres to walls, since it is easily dislodged.
Oxidant concentration reduction
Oxidant reduction can be accomplished by adding inert gas to enclosed processes to reduce the oxygen concentration to a level below that required for ignition to occur. This process, commonly referred to as inerting, is frequently used to protect grinding, mixing, pulverizing, storage and other enclosed operations. The physical and chemical properties of the combustible materials involved will govern the type and required purity of the purge gas needed. Both batch and continuous methods of inerting are available. When oxidant reduction is such that it presents an asphyxiation hazard, the area should be provided with signage to warn of the hazard and access should be restricted.
Batch inerting is typically used in mixing processes where the inerting case is drawn into the process by a vacuum system. Once the mixture is processed, the contents are transferred to the next processing step and the inerting gas is liberated from the batch vessel. This process typically will insert a fixed volume of gas based on the contents.
Continuous inerting is used where the explosive material is always being drawn from the container, such as a hopper or vat. These systems require a constant feed of inerting gas into the containment vessel to adjust for the changing volume of the combustible products. This changing volume requires that the system be monitored regularly to ensure that the maximum oxygen level is not exceeded. For example, the maximum oxygen level for cornstarch should not be permitted to exceed nine percent. Annex C of NFPA 69 can be used to determine the minimum oxygen level needed to support dust combustion. Monitoring should be performed in multiple locations to ensure that system configurations have not caused hazardous concentrations to form. Additionally, inerting does not eliminate the need for fire and explosion prevention measures. Operation of a system with an oxidant concentration low enough to prevent deflagration does not mean that incipient fires are prevented.
Mitigation/control
There are four primary methods of explosion mitigation and control. They are containment, isolation, venting, and suppression. While NFPA 69 discusses pre-deflagration detection and control systems as part of the mitigation process, these systems are used in conjunction with other prevention and protection systems. Generally, the detection and control systems are used to initiate some other protection equipment or process.
Containment
Equipment can be designed to be pressure-resistant or pressure-shock-resistant. Pressure-resistant equipment is designed and constructed to withstand specific pressures without deforming or rupturing. While pressure-shock-resistant equipment will also contain the explosion pressure, the explosion may permanently deform the equipment.
The use of pressure-resistant process equipment is generally limited because of high equipment costs. Generally, containment systems are only used in particularly vulnerable locations, such as where solids being handled are highly toxic or extremely valuable. When pressure is applied to a containment vessel with attached equipment, the shock imposed on the attached equipment, by the sudden change in internal pressure, can transmit a shock force to external equipment. As such, the attached equipment should be designed for these expected forces or provided with shock-resistive mountings to avoid damage to the equipment or the containment system.
Containers and vessels for pressure containment should be designed in accordance with the requirements of Section VIII of the International Boiler and Pressure Vessel Code, published by the American Society of Mechanical Engineers (ASME). Attention should be given to the methods by which the contained pressure will intimately be released from the containment system. While cooling of the explosive gases will relieve much of the pressure, care must be taken to return the internal pressure to ambient before allowing the process to continue.
Isolation
Isolation is accomplished by separating dust-producing processes from other plant operations and isolating interconnected processing units from each other, using barriers or chokes. The objective of explosion isolation is to prevent dust explosions spreading from the primary explosion location to other process units, workrooms and other areas. The location of dust-producing processes should be considered with care. Areas where combustible dusts are processed or handled should be segregated, separated, or detached from other operations or occupancies. Under no conditions should dust-producing operations be located in basements or the lower stories of a multi-level building.
Interconnected equipment should be isolated from each other to prevent the propagation of flame fronts and other conditions (i.e., fuel, oxygen, ignition sources, etc.) that might increase the size or duration of the event. Typical techniques used to isolate vessels include rotary valves, automatic fast-acting valves, flame front diverters, and other passive and active techniques to ensure that explosions do not propagate between interconnected equipment. Typically found in pipe and duct systems, these devices act to cut off the flow of combustible product and the flame or explosion front from entering an uninvolved area.
Venting
A deflagration vent is an opening in an enclosure through which burned and unburned materials expand and flow. Vents can be used to relieve pressure within plant units in the event of an explosion. The rate of pressure rise is an important parameter for venting a deflagration. A rapid rate of rise means that only a short period of time is available for successful venting. In terms of vent area, the more rapid the rate of rise, the greater the area needed for venting. Types of pressure relief devices include bursting panels, sheet diaphragms, bursting disks, pop-out panels, hinged explosion panels (i.e., doors), and spring-loaded vent covers. They may be designed for single use or for repeated use.
Pressure venting will generally be accompanied by the discharge of large quantities of burning dust, unburnt mixtures and combustion gases. To prevent this discharge from causing additional damage, it should be directed away from areas where individuals are likely to be working or passing and an isolation zone should be established. The design of venting systems for deflagrations is covered in detail in NFPA 68, Guide for Venting of Deflagrations.
Suppression
Automatic explosion suppression systems are active, comparatively sophisticated methods of explosion control, which are designed to prevent the creation of unacceptably high pressure by gas or dust explosions within enclosures that are not designed to withstand the maximum explosion pressure. They are generally used when less expensive methods cannot be applied.
Explosion suppression systems consist of a sensor system that will detect an incipient explosion and activate extinguishment devices. When activated, the extinguishing medium is injected into the enclosure, quenching the flames, and limiting the pressure buildup. Explosion suppression can be used to protect a variety of processing and materials handling equipment under a wide range of conditions. Explosion suppression cannot be used in enclosures where the suppressant cannot be effectively distributed.
Recommendations
The characteristics of combustible dust, the environment in which they are liberated, and the potential ignition sources found should be evaluated to determine the most effective method to protect a property from dust explosions. The following are general recommendations that can be used to reduce the hazards posed by dust explosions.
General
- Facilities that have equipment that creates or processes dust should perform an evaluation of the dust hazard present for both flash fire and dust explosion potential.
- Areas where combustible dusts are processed or handled should be segregated, separated or detached in such a manner as to minimize damage to other portions of the plant should an explosion occur.
- Good housekeeping is important to prevent dust accumulations. Vacuum cleaning is generally preferable to brushing or blowing the dust from horizontal surfaces.
- Blowing of dust using compressed air or steam can be performed when cleaning areas that are inaccessible or where other cleaning methods present a greater risk. However, when blowing of dust is performed, traditional vacuuming should be used to first reduce dust concentrations, compressed-air nozzles should be designed to limit the discharge gauge pressure to 30 psi (207 kPa), and ignition and heat sources should be eliminated.
- Employees should be informed of the hazards in their work area and trained to protect themselves from the hazards. The training should include instruction on what they are to do in an emergency.
Building construction
- Buildings in which materials that produce combustible dusts are stored, handled or processed should be of non-combustible or damage-limiting construction.
- Operations involving combustible dusts should be conducted in buildings of one-story construction, whenever possible. When multi-story construction is used, operations representing the greatest explosion hazard should be conducted on the uppermost floor or isolated from the rest of the building.
- Beams, ledges, flat and wide ductwork and other structural features where dust may settle should be limited.
- Floors and load-bearing walls exposed to dust hazards should be designed to preclude failure during an explosion.
- Buildings of pressure-resistant construction should be provided with explosion venting appropriate to the anticipated pressures produced by the dust hazard.
Controlling ignition sources
Separating ignition sources from areas where explosive atmospheres may form will reduce the risk of explosion considerably. The methods used will vary depending on the source of ignition. They include the following:
- Isolating or shielding hot surfaces.
- Removing foreign objects from process streams.
- Designing belt drives to stall without slipping.
- Properly aligning and mounting rotating equipment to eliminate vibration and overheated bearings.
- Using properly classified electrical equipment, including lift trucks, for the area and condition.
- Using conductive materials and coatings for all plant items that may accumulate large static charge densities.
- Grounding conductive equipment.
Systems that detect and extinguish sparks or embers may be used to augment ignition control programs. Such systems operate by means of detectors that sense the radiation of a hot or glowing particle and actuate a special extinguishing system that quenches the particle.
Equipment
- Equipment should be substantially constructed and be as dust-tight as possible. Special precautions are required for some equipment, such as the use of magnetic separators, to prevent metal objects from entering grinding equipment.
- Electrical equipment used in potential dust-hazard areas should conform to the NFPA 70, specifically equipment for Class II locations, such as combustible dust areas.
- In areas containing a combustible dust hazard, only industrial trucks of a type suitable for the electrical classification of the area should be used.
- All conductive equipment, including ductwork and drive belts, should be protected from static hazards by permanent electrical grounding and bonding.
- Explosion suppression systems should be provided and designed in accordance with NFPA 69.
- Dust extraction and control systems should be provided and designed in accordance with NFPA 91.
Fire protection
- Portable fire extinguishers capable of extinguishing combustible dust fires should be provided throughout the process area.
- Automatic sprinkler protection should be provided in all buildings or rooms in which the storage, handling or processing of combustible dusts is conducted.
- Spray or fog nozzles should be provided for hose stations and extinguishers to reduce the potential of dust being thrown in suspension.
Frequently asked questions
This section provides answers to some commonly asked questions regarding the storage, handling or processing of combustible dusts.
Materials
Often, work sites have questions regarding specific types of dust and if it would present an explosion hazard. The following are some common questions related to specific dusts:
Is there a fire or explosion hazard associated with aluminum dust?
Aluminum dust can be explosive depending on the particle size and the alloy composition. The finer the dust, the more easily it can be ignited and the greater the explosion severity. Aluminum dust has an ignition temperature of 420°F (215°C), with a median explosive particle size of less than 10 µm. Explosive concentrations can occur at as little as 0.05 oz./ft.3 (50 g/m3). When suspended in a cloud, aluminum dust has an explosive pressure rate-of-rise greater than 22,000 psi/sec (151,668 kPa/sec).
NFPA 484, Standard for Combustible Metals, Metal Powders, and Metal Dusts, provides information relating to fire and explosion protection for aluminum dust environments. Some of the key elements of an effective fire/explosion prevention plan for aluminum dust include:
- Scoops, shovels and other tools used in an area where aluminum dust is present should be non-conductive and spark-resistant.
- Electrical equipment in potential dust-hazard areas should conform to NFPA 70 for Class II locations.
- Powered industrial trucks, such as forklifts and scissor lifts, should be listed/approved for use in Class II locations.
- Only Class D fire extinguishers should be used in areas where dry combustible aluminum dust is present.
Dust collection systems should be specifically designed for aluminum dust and not utilized for any other dust collection. Minimum considerations include:
- The dust collection system, transfer pipes, and related components should be designed in accordance with NFPA 91.
- All components of the collection system should be bonded, grounded, and designed to prevent condensation from forming.
- Dust collectors should be located outside of the building.
- Dust collectors should be provided with explosion venting designed in accordance with NFPA 69.
- Aluminum dust should be removed from the collector at least daily.
Do stainless steel dust and similar iron dusts present an explosion risk, similar to that of aluminum?
While not as volatile as aluminum dust, steel dust does have the potential to propagate an explosion under certain conditions. There are several references that provide information relating to the dust concentrations required to present an explosion hazard. For example, on average, these references indicate that 0.045 oz./ft.3 (0.04 kg/m3) of aluminum dust is the minimum concentration required to propagate an explosion; in comparison, the minimum concentration required to propagate an explosion in steel is 0.1 oz./ft.3 (0.1 kg/m3). This makes iron and steel less of a hazard than aluminum, but still capable of producing an explosion.
Many business owners do not realize the combustibility of finely divided steel particles. A demonstration of the combustibility of finely divided steel particles can be performed using steel wool. If an ignition source (i.e., torch) is applied to a steel wool pad, it will burn rapidly. If the same pad is pulled apart to make it have a larger surface area, the fire spread will increase exponentially, based on the increase in the surface area. Likewise, if those particles are reduced to a dust and liberated into air, the rapid burning will result in a rapid release of energy in the form of an explosion. Loss prevention activities for this exposure include the control of ignition sources, the use of dust collection equipment, and routine housekeeping.
What are the fire/explosion hazards related to Polyvinyl chloride (PVC) dust?
Polyvinyl chloride (PVC) is a thermoplastic compound that softens when heated. In its solid form, PVC can be difficult to ignite and generally will self-extinguish when the heat source is removed. However, as with most finely divided particles, PVC dust ignites readily and burns rapidly. When PVC burns, it releases hydrogen chloride that is both toxic and corrosive. The explosion hazard of a combustible dust, including PVC, is similar to the explosion hazard of a flammable liquid vapor or flammable gas (i.e., an ignitable mixture must be present before an explosion can occur). The primary difference is that dust must be suspended in air before an explosion can occur. Tests have shown that PVC dust with a median particle size of 25 µm and a minimum concentration of 125 g/m3 (0.24 oz./ft3) can explode.
Housekeeping procedures should be developed to ensure that explosive concentrations of PVC dust are not present in the work area. Electrical equipment in potential dust-hazard areas should meet the requirements of NFPA 70. For additional information, see Business Links Report BL-40-06, Plastic Processing, through our Risk Solutions Partner, E&S.
Does soy dust have the same fire/explosion hazards as starch or wheat dust?
Yes. Soy dust can pose a dust explosion hazard. NFPA 61 lists explosive test data for soybean dust in Table A.6.2.1. While the minimum explosive concentration of soybean dust (200 g/m3) (0.19 oz/ft3) required to propagate an explosion is much higher than that for grain dust (i.e., minimum concentration for wheat dust is 60 g/m3) (0.06 oz/ft3), there is still the potential for an explosion to occur. Depending on the median dust particle size, moisture content, airborne concentration and the available ignition sources, the blast force potential for soy dust is comparable to wheat dust.
Does fiberglass present a dust explosion hazard in a manufacturing process, such as making hot tubs?
Fiberglass is not listed in NFPA 499, which provides a listing of dusts that present an explosion hazard when liberated in air. Further, fiberglass is not included in Dust Explosions in the Process Industries, 2nd Ed., Oxford, UK, 1991, which provides a comprehensive listing of dust explosion tests and derived data on more than 200 materials.
However, just because fiberglass is not considered a combustible dust does not mean that there is no dust hazard present. A review of the chemicals used in the manufacturing process to bind the fiberglass to molds or forms should be performed. It is very possible that the additives present a dust explosion hazard.
For example, on February 20, 2003, an explosion and fire damaged a manufacturing plant in Corbin, Kentucky, fatally injuring seven workers. The facility produced fiberglass insulation for the automotive industry. According to the U.S. Chemical Safety Board (CSB), the explosion involved resin dust that accumulated in a production area and was ignited by a faulty oven. The resin involved was a binder used in producing fiberglass mats.
Does grass seed dust present a fire/explosion hazard; does its presence require classified electrical equipment?
Grass dust is a combustible material and, as such, operations involving the development of grass dust should adhere to the requirements of NFPA 61, Standard for the Prevention of Fires and Dust Explosions in Agricultural and Food Processing Facilities. Chapter 13 of NFPA 61 requires electrical wiring and equipment to meet the classification requirements of NFPA 70. NFPA 70 requires electrical equipment used in potential dust-hazard areas to be listed for use in Class II locations; however, NFPA 61 does provide an exception to this requirement for when equipment is listed as intrinsically safe or as purged and pressurized enclosures for electrical equipment.
In addition to providing appropriately classified electrical equipment, other ignition sources should be removed from areas where explosive atmospheres may form. The methods to control these ignition sources will vary depending on the source of ignition. As with any other hazardous environment, heated surfaces, sparks and static discharges should be eliminated. Regular inspection, testing and maintenance of equipment is vital to proper operation and the prevention of fires. Procedures for controlling workplace ignition sources, such as smoking, welding and cutting, should be addressed in a formal fire prevention plan.
Collection equipment
Often, work sites have questions regarding specific types and configurations of dust collection equipment, such as vacuums, duct work and dust bags. The following are some common dust hazards collection equipment questions:
Are there any requirements for a vacuum hose that is used to clean up dust?
Yes. NFPA 77, Recommended Practice on Static Electricity, provides information on vacuuming of dusts (i.e., pneumatic transport systems) in subsections 9.6 and 9.7. Subsection 9.7 requires flexible hoses to be made of “nonconductive material that incorporate a spiral stiffening wire” that “contacts the metal end couplings and that the end couplings make a good connection to ground.” Vacuums and related hoses should comply with UL 1017, Standard for Safety Vacuum Cleaners, Blower Cleaners, and Household Floor Finishing Machines, published by Underwriters Laboratories Inc., and be approved for use in Class II Division 1 environments.
Is there a safe method to remove dust from beams when vacuuming is not possible, such as by blowing with air guns?
Good housekeeping should be practiced as a means of reducing the hazard in areas where the potential for a dust explosion exists. Plant surfaces should be regularly cleaned to prevent the accumulation of dust. Very little dust, suspended in air, is required to produce uniform dust clouds within the explosive range of most dusts. As such, most loss prevention guides recommend a cleaning frequency to prevent any accumulations greater than 1/8”. Vacuum cleaning is preferable to brushing or blowing the dust from horizontal surfaces. To facilitate cleaning and minimize dust accumulation, interior surfaces should be made as smooth as possible and window ledges, girders, beams, and other horizontal surfaces designed to minimize deposition of dust.
Factory Mutual Engineering (FM) offers recommendations for dust control in paragraph 2.2.4 of Loss Prevention Data Sheet 7-76, Prevention and Mitigation of Combustible Dust Explosion and Fire. The paragraph recommends vacuuming as the preferred method of dust removal. However, when vacuuming is not possible, the paragraph offers alternative cleaning options including:
- Damping the dust and then removing by sweeping
- Water wash down of dust
There is a provision in the data sheet for situations where “air blow-down” is the only method available for cleaning. The steps include: control of ignition sources, use of low volume, low pressure air, and a frequent cleaning schedule to reduce the amount of dust suspended in the air during the cleaning process. The FM Data Sheet can be downloaded from Factory Mutual’s website at www.fmglobal.com.
Can polyvinyl chloride (PVC) pipe be used as ducting for a wood shop dust collection system?
No. Paragraph 8.2.2.2.1.2 of NFPA 664, Standard for the Prevention of Fires and Explosions in Wood Processing and Woodworking Facilities, specifically prohibits the use of “nonconductive material, such as PVC pipe,” as ducting in dust collection systems. NFPA 664 requires ductwork be metallic, except for short sections of flexible ducting needed to connect the machine and the collection system. An annex note to 8.2.2.2.1.2 further clarifies that a ground wire or other grounding system is not acceptable for creating a conductive path across PVC pipe.
Dust displaced from a surface on which it rests may generate a significant charge, such as moving through a pipe. The total charge developed depends on the chemical composition of the material, the size of the particles, and the amount of surface contact. Charge generation seldom occurs if both the dust and the surface on which it rests are conductors. However, it is likely to occur if one material is a conductor and the other is a nonconductor, like PVC. PVC’s natural insulating ability can lead to a buildup of static charges when the moving wood dust comes into contact with the surface of the pipe. Once the charge is created, the concern then becomes static discharges. When combustible dust is suspended in air and subjected to a static discharge, an explosion can occur.
Where can I find requirements for dust collection systems for woodworking operations, such as pallet recycling and scraping?
Pallet disassembly band saw dust collection systems should meet the requirements of NFPA 664. There are two typical configurations for dust collectors: a one-stage and two-stage system. In the one-stage system, the airflow is brought into the collector, heavy particulate falls to the bottom, dust-laden air moves though the filter bags, leaving the dust on the bag and the discharged air is returned to the facility or the atmosphere. In a two-stage system, the same event sequence occurs but a cyclone is used to separate heavier particulate, then the dust-laden air is directed through a separate bag house. In either case, the primary fire protection focus is to prevent the introduction of sparks and embers into the collector.
To prevent a fire or dust explosion, sparks and embers need to be prevented from entering the bag house. This is typically achieved by including spark and metal detectors on the dust collection system in-feed, high-speed spark detectors in the duct work and automatic-damper (tied to the detection system) gates before the bag house.
If a spark or ember does enter the bag house, four typical events can occur:
- The ember burns out without causing a fire or explosion.
- The ember falls to the bottom of the collector and ignites the dust.
- The filter media can be ignited, burn, and fall to the bottom of the bag house.
- The filter media is ignited and burns through, resulting in a pressure drop in the bag house. This often leads to a dust concentration that is explosive.
In all cases, the risk control measure is to prevent the introduction of the ignition source into the environment. The installation of high-speed spark detectors interlocked with the air handling system’s flame detectors, automatic sprinklers inside the bag house and explosion venting are the most effective methods to reduce losses in these environments.
The use of heat detectors, fixed or rate-of-rise, to activate suppression and air control systems should be considered. If an ember is drawn into the bag house when the airborne dust concentration is above the explosive limit, there is an increased potential for a deflagration to occur (assuming that the ember has sufficient energy). In this case, a heat detector will not afford the property owner any early warning.
If the concentration is insufficient for an explosion, then a fire condition may occur. This condition would warrant a device to activate suppression equipment and activate building fire alarms. A rate-of-rise detector usually requires at least a 10°F (5.6°C) temperature change to operate. This would require that the combustion process produce in excess of 100 BTU/sec to initiate a signal transmission. If a smoldering fire occurs, the heat release rate combined with the airflow through the collector would be insufficient to trip a detector. The same concern would apply to flaming combustion; the amount of airflow through the collector would prevent a "rate-of-rise" condition of sufficient dynamic to trip the detector.
The most comprehensive control process would be the installation of high-speed spark detectors and air handling controls before the bag house, a flame detection system in the bag house, and explosion venting. All of these should be integrated into a suppression system to control both the ducts and the bag house. Installation of flame detectors inside the bag house should be designed and installed to provide full coverage of the occupied space. The layout should be performed by a qualified fire protection installer using actual measurements of the space.
Is it acceptable to return air from a dust collector into the building of origin?
Yes. The bag house air can be returned to the building under certain conditions. Such conditions are provided in Subsection 2.1.3 of NFPA 654. This subsection allows return air to enter a building only if the separator (i.e., the bag house) is designed to remove the dust from the air, with an efficiency of 99.9 percent. In addition, Subsection 3.6.4 of NFPA 654 requires that the building be designed to prevent the energy from an explosion in the bag house from entering the building. Isolation protection, such as blast gates, dampers or abort gates, should be placed in ducts where the ducts pass through a physical barrier, such as a wall, that serves to separate an area from an explosion hazard. These isolation devices are usually activated by a spark or flame detector or other fire protection system.
Chapter 8 of NFPA 664 provides specific requirements for protecting bag houses in woodworking operations. Subsection 8.2.2.6 of the standard allows for bag house air to be returned to the building under certain conditions, including:
- The system is provided with a listed spark detection system between the last point where material can enter the system and before the bag house.
- Return-air ducts are provided with high speed abort gates that are activated by the spark detection system.
- A manual reset device is provided for the abort gates (automatic resets are not allowed by code).
Fire protection
Does NFPA require furniture manufacturers and similar risks to provide automatic sprinkler protection for wood dust-collection equipment?
No. NFPA 664, published by the National Fire Protection Association (NFPA), requires that dust collection equipment posing fire and deflagration hazards be protected; however, this protection does not have to be by automatic sprinklers. There are other protection methods that are acceptable. The requirements for fire protection of dust collectors and associated ductwork are found in Chapter 8. The requirements vary depending upon the type of equipment and severity of hazard. There are multiple options to control these exposures, including the use of suppression systems. Additional controls may include spark detection and abort gate systems, flame-quenching devices, and explosion venting, or location out of doors. When automatic sprinklers are used to protect a dust collector, Subsection 8.2.2.5.2 requires the system to be hydraulically designed to provide a minimum density of 0.20 gpm/ft2 (72 L/min/m2).
Summary
The control of dust explosions is a dynamic process that requires close attention to both the fuel source (i.e., dust) and the ignition source. Like the explosion hazard of flammable vapor, attention must be given to controlling the buildup of dust to a level that will support flame propagation, while ensuring that such a concentration is not given an ignition source. The most effective explosion prevention system will use redundant safeguards to (1) eliminate the production of dust, (2) confine any dust produced to a safe area, (3) prevent the development of ignitable dust concentrations, and (4) control ignition sources.
References
- Eckhoff, R.K. Dust Explosions in the Process Industries. 3rd ed. Burlington, MA: Elsevier, 2003.
- Engineering and Safety Service. Static Electricity. FP-70-08. Jersey City, NJ: ISO Services, Inc., 2016.
- Factory Mutual Engineering Corp. “Prevention and Mitigation of Combustible Dust Explosions and Fires.” Property Loss Prevention Data Sheet 7-76. Norwood, MA: FM Global, 2017.
- National Fire Protection Association (NFPA). Fire Protection Handbook. 20th ed. Quincy, MA: NFPA, 2008.
- ––. Guide for Venting of Deflagrations. NFPA 68. Quincy, MA: NFPA, 2013.
- ––. National Electrical Code. NFPA 70. Quincy, MA: NFPA, 2017.
- ––. Recommended Practice for the Classification of Combustible Dusts and of Hazardous (Classified) Locations for Electrical Installations in Chemical Process Areas. NFPA 499. Quincy, MA: NFPA, 2017.
- ––. Recommended Practice on Static Electricity. NFPA 77. Quincy, MA: NFPA, 2014.
- ––. Standard for Exhaust Systems for Air Conveying of Vapors, Gases, Mists, and Noncombustible Particulate Solids. NFPA 91. Quincy, MA: NFPA, 2015.
- ––. Standard for the Prevention of Fire and Dust Explosions from the Manufacturing, Processing, and Handling of Combustible Particulate Solids. NFPA 654. Quincy, MA: NFPA, 2017.
- ––. Standard on Explosion Prevention Systems. NFPA 69. Quincy, MA: NFPA, 2014.
To learn more about Hanover Risk Solutions, visit hanoverrisksolutions.com
Copyright © 2018, ISO Services, Inc.
The recommendation(s), advice and contents of this material are provided for informational purposes only and do not purport to address every possible legal obligation, hazard, code violation, loss potential or exception to good practice. The Hanover Insurance Company and its affiliates and subsidiaries ("The Hanover") specifically disclaim any warranty or representation that acceptance of any recommendations or advice contained herein will make any premises, property or operation safe or in compliance with any law or regulation. Under no circumstances should this material or your acceptance of any recommendations or advice contained herein be construed as establishing the existence or availability of any insurance coverage with The Hanover. By providing this information to you, The Hanover does not assume (and specifically disclaims) any duty, undertaking or responsibility to you. The decision to accept or implement any recommendation(s) or advice contained in this material must be made by you.
LC DEC 2018-338
171-1751 (11/18)