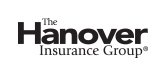
Developing a safety program for contractors
Getting started
Just having a written safety program will not guarantee that your company job sites will be incident free. A commitment must be made by management to fully implement the program company wide. A written safety program shows your company is committed to managing the resources it has, including workers, company equipment and capital. By managing these resources, your company can control the costs associated with losses. You may also find that workers are more productive, due to an increase in confidence obtained from feeling protected from hazards and that the company is concerned about their safety.
Assessing your current safety performance
A good starting point would be to review data on your past insurance claims with your Risk Solutions representative. Include in your review all incidents, not just those associated with employee injuries (workers’ compensation) since damage to equipment or property indicates a safety improvement opportunity. Be aware of any indicators that show trends: for instance, four eye injuries over the past few years could indicate that personal protective equipment (PPE) may not be available or its use may not be enforced.
Talk to supervisors and employees about any incidents that almost resulted in a claim or accident. You should also consider performing several job site inspections and then compare them to determine if there are potential safety issues that are common at your job sites. Review past insurance reports and discuss findings with your Risk Solutions representative. All of these assessments can help in determining where there are gaps in your current safety program that need immediate attention.
Who develops the program?
Some companies have a full-time safety manager/coordinator/director and this person would be the logical choice to oversee development of the program. Several organizations offer sample safety programs that can be downloaded and used as a reference. Whoever develops your program should be familiar with the type of work you perform and the OSHA standards that apply. Other options that may be considered are:
- Selecting one of your current employees to be the safety coordinator. It is important to ensure they get the management support, information and training needed to be successful in fulfilling their new responsibility.
- Hire a consultant with the knowledge and experience in your industry to guide your company in developing your program. Consultants can be retained to develop the full program or provide input and recommendations that can save time and ensure the program meets your safety responsibilities.
- Work with your Risk Solutions representative who can provide guidance on how to implement your program.
- Designate a safety management team (safety committee) to develop the program. An advantage here is the safety committee can also champion the program in the field.
The safety budget
While developing written policies is fairly straightforward, implementing the program will require a financial investment. Safety practices are only effective when:
- Employees are trained on how to work safely.
- Time is allowed for job site inspections and oversight of the program in the field.
- Professional development training is provided for the designated safety coordinator and supervisors.
How to win support for your new program
Management support
Getting management support is critical to the success of any safety program. Management should understand that the financial investment of preventing accidents is a good business decision and will be less costly than having an accident. Management should understand that accident costs go beyond just medical payments or equipment repair (direct costs), but also include time spent by company staff in filing claims, finding replacement workers/equipment and lost production (indirect costs). Several studies have reported that for every dollar spent on direct costs $4 to $15 is spent on indirect costs. Another way to look at this is to use your company profit margin to determine how much work would have to be awarded to pay for accidents.
YEARLY ACCIDENT COSTS | PROFIT MARGIN AND AMOUNT OF WORK / SERVICES NECESSARY | |||
---|---|---|---|---|
1% | 2% | 5% | 10% | |
$1000 | $100,000 | $50,000 | $20,000 | $10,000 |
$5000 | $500,000 | $250,000 | $100,000 | $50,000 |
$10,000 | $1,000,000 | $500,000 | $200,000 | $100,000 |
$25,000 | $2,500,000 | $1,250,000 | $500,000 | $250,000 |
Worker support
The best way to ensure that the safety program will be successful is to involve all company employees in the development of the program. Seek employee input at every stage of development so your program doesn’t become just another set of rules.
In many cases, your employees know the hazards of their work better than you do and they may point out hazardous work tasks that should be changed or improved. Many of your employees may also be interested in and capable of leading safety training sessions. Using experienced workers who have been there to discuss why safety measures are important can enhance buy-in by other employees.
Responsibilities
Assigning responsibility to all employees in the company makes everyone accountable for safety and requires a team effort to be successful. Responsibilities are not just for workers in the field, as they do not have the ability or resources necessary to implement all aspects of the program. Additionally, as already discussed, management must support the program and that can only occur by assigning them responsibilities. Consider the following recommended responsibilities:
The company president will:
- Provide direction, motivation and accountability to ensure an effective safety program for all company locations and job sites.
- Provide for home office and field administrative safety activities in keeping with the company’s safety goals and objectives.
- Establish an adequate budget to fund the safety program for all departments and job sites.
- As part of performance evaluations, hold supervisors and superintendents accountable for the success or failure in achieving specified targeted company safety performance and insurance cost control goals.
- Assist supervisors and superintendents in the formulation of department and job site-specific safety programs.
- Assure that each member of the company supervisory team has a good working knowledge of all company, client and governmental safety requirements.
- Periodically take part in various employee training sessions.
- Review monthly safety status reports for the purpose of evaluating the company’s safety and insurance performance.
Supervisors
The supervisor/superintendent and foreman are responsible for the safety of all company employees working on their job site.
Supervisors will:
- With the assistance of the president, establish project safety, health, first aid, fire prevention and protection, site security and insurance claims handling programs that comply with applicable company and client contractual documents and specifications, federal or state OSHA standards and company safety and loss control procedures.
- Monitor the safety status of their department job site and employee morale by personally conducting a daily safety inspection of the entire work location and initiating needed corrective action by responsible supervision.
- Conduct accident investigations, analyze the causes and formulate recommendations for corrective and preventative action.
- Conduct safety training for field employees based on the work hazards they may encounter.
- Assure that each job site has the necessary safety equipment and protective equipment necessary for the work.
- Monitor the safety performance of all subcontractors to assure compliance with the safety performance requirements of the company and job site.
- Conduct job site safety meetings and answer employee questions regarding safety requirements.
- Conduct safety orientations for new employees.
- Enforce company and job site safety rules.
- In the case of any serious accident or OSHA inspection, notify the company president as soon as possible.
Employees
Each employee should be expected, as a condition of employment, to work in a manner which will not inflict self-injury or cause injury to fellow workers. It is important that each employee understand that the responsibility for his or her own safety is a job requirement.
Each employee will:
- Comply with all safety rules and regulations that apply to his or her own department or trade.
- Report all accidents and injuries immediately.
- Obtain the proper tools and personal protective equipment for the job at hand.
- Report all unsafe conditions to a supervisor in charge.
- Know what emergency telephone number to call in case of fire and/or personal injury.
- Help to maintain a safe and clean work area.
Accountability
Once responsibilities have been assigned, a method must be put into place to assure that the responsibilities are acted upon.
Each employee must be held accountable for their safety performance by their supervisor and supervisors must be held accountable by the company. The most proactive method is to establish accountability procedures. These procedures must be applied consistently and fairly to all levels of company employees. A safety program will fail if some employees are allowed to break safety rules because they are productive workers or get the job done by any means possible. One way to do this is to assign safety performance as a percentage of yearly incentive programs. Evaluating how involved supervisors were in implementing the safety program, such as conducting job site safety meetings, performing job site inspections and results of safety audits should all be weighted (given a percentage). When calculating yearly incentive bonuses the safety percentage could be used to determine the final bonus. For supervisors not achieving the safety goal, a deduction is applied to final incentive bonus amount.
Implementing the program
For many companies the thought of putting together a safety program is accepted as a good idea but just having a program does not mean safety goals will be met. Many safety programs are not fully implemented in the field and soon become just another binder on the shelf.
Implementing the safety program means that the rules for work are communicated to the field, inspections are performed to evaluate compliance of those rules and all employees are trained to perform safely around the hazards they encounter. It is also important to establish that all workers have the authority and responsibility to correct and report unsafe conditions, even if they are not exposed to the hazard. This will require supervisors to encourage reporting and actively investigate the nature of the hazard to determine why the condition exists. This may require the work to stop until the condition can be corrected and that decision must also be supported by the company.
Safety enforcement procedures
When it is necessary to warn an employee of an infraction of company safety rules, a written reprimand should be issued on a company employee warning form for proper documentation. When violations of safety rules occur, act immediately to correct the situation and alert other employees that these risks will not be tolerated.
By requiring safety as part of their ongoing work responsibilities, your employees will see that the company is interested and concerned about their wellbeing and not just profit. Enforcement procedures show that the company is serious about the program and a written warning offers notice to the employee that they are expected to follow the guidelines. Many companies use a multiple infraction format for enforcement:
- First infraction—written warning
- Second infraction—time off without pay
- Third infraction—termination
Termination should also be considered for gross misconduct, where the action of the worker could have resulted in a serious accident or major property damage.
Prior to issuing such a ruling, it is essential that your human resource department has been involved and it has been determined that the worker knew they were violating a company rule and were trained in the proper procedures.
Establishing safety requirements
The company safety program should contain the safety requirements that apply to the work activities performed on the job. A good starting point is to compile the common work activities (exposures) that are performed, identify the hazards and establish what the company will do to prevent an incident (safe controls). When deciding what requirements will be followed, a company has several options:
- Using OSHA standards as the bare minimum for being in compliance with federal/state safety laws
- Using standards established by the American National Standards Institute (ANSI) and other safety associations as best practice.
- Establishing company safety rules that are more restrictive then the OSHA/ANSI standards.
Reviewing and updating your program
Once your safety program is written, it is important to periodically review it to ensure the procedures are effective and goals are met. At least annually, review your company’s safety progress by reviewing insurance claims and inspections, incident reports, job site safety audits, supervisor safety reports and training needs. Also ask employees for any suggestions they have to improve the overall safety program. This is another good reason to establish a company safety committee for their input. A summary report to management on safety activities and the positive results in managing company resources and controlling costs will also help in their continued support.
Ten steps in developing a comprehensive safety program
- Define your needs:
- What are the hazards of normal and unusual or infrequent company operations?
- What are the company’s insurance and legal risks?
- What are the usual construction client safety specifications, if any?
- Define your safety goals.
- Write your policy.
- Establish the budget.
- Identify the person(s) who will carry out the program.
- Set standards for employee accountability and disciplinary action.
- Distribute safety policy and work rules to all employees.
- Educate and train all employees in particular safety responsibilities.
- Perform daily duties under the program.
- Routinely audit and evaluate program effectiveness.
Additional resources
OSHA Safety and Health Management eTool
OSHA “Safety Pays” Calculator to assess costs of injuries
OSHA Compliance Assistance Quick Start
Hanover Risk Solutions Website
To learn more about Hanover Risk Solutions, visit hanoverrisksolutions.com
Reference: 29 CFR 1926.20(b) Accident prevention responsibilities
The recommendation(s), advice and contents of this material are provided for informational purposes only and do not purport to address every possible legal obligation, hazard, code violation, loss potential or exception to good practice. The Hanover Insurance Company and its affiliates and subsidiaries ("The Hanover") specifically disclaim any warranty or representation that acceptance of any recommendations or advice contained herein will make any premises, property or operation safe or in compliance with any law or regulation. Under no circumstances should this material or your acceptance of any recommendations or advice contained herein be construed as establishing the existence or availability of any insurance coverage with The Hanover. By providing this information to you, The Hanover does not assume (and specifically disclaims) any duty, undertaking or responsibility to you. The decision to accept or implement any recommendation(s) or advice contained in this material must be made by you.
LC JAN 2019 12-380
171-1106 (11/14)