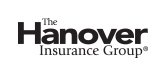
Controlling the business interruption exposure
While businesses cannot totally prevent the occurrence of disasters, the keys to controlling business interruption losses are to have plans in place to prevent or limit damage from a disaster and, in the event of a shutdown, to return the business to operation as soon as possible. This report provides information on factors to consider in assessing the risk of potential emergencies on a business and the development of strategies for controlling these risks.
Introduction
A business does not have to perform high-risk activities to be confronted with crisis. Any sort of emergency that happens suddenly, that disrupts the routine of the business, that hurts its competitive position, and that demands immediate attention can be called a crisis. Loss of electricity to an electronic data processing firm can be as damaging as a fire is to a factory.
Emergencies can be caused by many factors: physical perils, such as fires, floods or earthquakes; work accidents; loss of essential supplies and utilities, such as electricity; walk-outs or other labor problems; or deliberate acts of terrorism or sabotage. Some emergency situations give advanced warnings of several days, while others come totally unexpected. Emergencies also vary in degree and level of impact. Traditionally, large-scale or catastrophic emergencies are called disasters.
Preplanning is essential for successfully minimizing any adverse effects of an emergency on a business and its operations. Being unprepared can cause a business to experience significant loss of assets or human life or to experience business interruptions. Also, being prepared for "expected" emergencies will make a business better suited to deal with unexpected or unforeseeable ones.
Business interruption insurance can also be vital to the survival of a business. If a catastrophe, such as a fire, causes a business premises to be temporarily unusable, the business may have to temporarily relocate or even close. A business that must close completely while the premises are being repaired may lose revenue to competitors. A quick resumption of business after a disaster is essential. While the business’s property insurance pays to repair or replace damaged property, it does not protect the insured against consequential damages. Business interruption coverage fills that gap.
Business interruption insurance is designed to indemnify a business against losses arising from its inability to continue the normal operations and functions of the business. It covers profits the business would have earned, based on financial records, had the disaster not occurred; operating expenses, such as electricity, that may occur even if the core business activities are suspended; and it may cover expenses incurred from operating out of a temporary location while the original premises are being repaired.
Coverage is triggered by the total or partial suspension of business operations due to the loss, loss of use or damage to all or part of the buildings, plant, machinery, equipment or other business property as the result of a covered cause of loss. The causes of loss can include fire, natural disasters, collapse, vandalism, malicious mischief, riot, riot attending a strike and civil commotion.
Extra expense insurance reimburses the business for a reasonable sum of money that it spends, over and above normal operating expenses, to avoid having to shut down during the restoration period. Usually, extra expenses will be paid if they help to decrease business interruption costs.
There are many words used to describe emergency preparedness — contingency planning, disaster recovery planning, crisis management, etc. The Occupational Safety and Health Administration (OSHA) requires companies to develop Emergency Action Plans, while the Environmental Protection Agency (EPA) requires Emergency Response Plans.
All these terms essentially describe ways of protecting the life, property, and assets of a business. “Contingency planning" and "crisis management" focus on preparing for, or responding to, an event. "Disaster recovery planning" focuses on restoring operations once a natural disaster has occurred. Emergency preparedness (EP) is a risk management philosophy concerned with anticipating, preparing for, responding to and recovering from any crisis or unforeseen event.
Emergency preparedness has one goal: to minimize the adverse effects of an emergency upon a business. This goal is accomplished by the creation of an in-house program to assess the risk of potential emergencies on a business and the development of a strategy for controlling those risks. The strategy is implemented through the development of an emergency preparedness plan. This plan spells out specific actions that should be taken before, during and after an emergency and assigns who is responsible for taking those actions.
Assessment
It is generally too late to plan an effective response after a disaster has struck and a shutdown has occurred. Effective contingency and disaster planning require that the business understand fully the exposures to its operations and the measures that can be taken to minimize the consequences of a disaster.
Factors to be considered in the assessment include:
- What is the history of natural hazards, such as flooding, hurricanes, tornadoes and lightning, in the area?
- Have the probabilities and consequences of internal and external events, including natural and man-made events, that could result in an interruption of the business’s operations been assessed and quantified?
- Does the business have contingency plans to respond to emergencies, such as equipment failures, fires, floods or natural disasters?
- Are contingency plans more focused on events with a relatively high probability of occurrence or with more severe consequences?
- In the event of a business interruption, have the resources needed to support critical business activities been identified and addressed in the contingency plans?
- Are employees trained in executing the contingency plans?
- Is the facility in compliance with local building and fire prevention codes?
- If the business is located in a multi-occupancy building, are operations in adjoining premises of a hazardous or high-risk nature?
- Have systems, such as electrical systems, HVAC/mechanical systems, and telecommunications systems, which are critical to the continued operation of the business, been identified and are they properly maintained and inspected regularly?
- Do fire protection systems, including automatic sprinkler systems, meet applicable codes and standards?
- Are fire safety inspections conducted on an ongoing basis?
- Does the business operate independently, or is it part of a franchise operation, such that a temporary business interruption could be handled by another business in the chain?
- Are the premises owned or leased?
- What is the financial condition of the business?
- What are the annual revenues for the business?
- Are important business records, both written and computerized, stored in appropriate record protection equipment and backup records stored off premises?
- Does the business depend on any single supplier for its raw materials or its main products?
- If the business experiences a peak season, what would be the effect if a loss occurred during this season?
Hazard analysis
A hazard analysis is done to identify and evaluate any hazards that may exist, determine the consequences of the hazards, and assess any potential risk. The purpose of these steps is twofold: to make sure that all crises are considered when preparing the response plan and to make sure that planning resources are allocated properly. The hazard analysis is critical to effective planning. It is pointless to waste time and money preparing for an event that will likely not occur or is of little consequence.
Hazard evaluation
Hazard evaluation has two steps: identifying any potential hazards and evaluating the frequency of likelihood of an occurrence. Typical hazards to be considered are:
- Fires or explosions
- Geological/meteorological occurrences: tornados, hurricanes, earthquakes, floods, weather extremes, lightning, etc.
- Work accidents: severe injury, multiple severe injuries, rumors, panic, etc.
- Utility outages: loss of electricity, heat, steam, refrigeration, gas, etc.
- Hazardous materials releases
- Bomb threats
- Civil disturbances: riot, strike, sabotage, terrorism, etc.
- Evacuations
Probability assessment
Once all potential hazards are determined, they must be evaluated in terms of their probability and frequency of occurrence. Numerous methods exist for determining the probability and frequency of an event occurring. They range from being very simple (e.g., qualitatively ranking events in terms of "frequent," "probable," "occasional," "unlikely," etc.) to the very complex (e.g., determining numerical probabilities for events occurring).
The method chosen will depend on the needs and sophistication of the company. Not everyone needs to perform complex probability assessments. The purpose of doing any of these assessments is to develop a realistic list of potential hazards that could affect a company, highlighting the most likely, and deemphasizing the least likely.
Consequence analysis
Once hazards are evaluated in terms of likelihood of occurrence, they should be evaluated in terms of the consequences of occurrence. A question that should be asked is, "If this event occurs, how will it impact the company, our employees, the environment and the surrounding community?"
As with probability assessments, there are numerous methods for making formal consequence assessments. A simple method is to look at the potential consequences of an event on personnel, property, the public and the environment and estimate the potential severity of the consequence in terms of "catastrophic," "critical," "marginal," "negligible," etc.
Risk assessment
Once all potential hazards are identified and their consequences determined, they should be evaluated in terms of the risk they present. Risk is generally defined as a measure of potential economic loss or human injury in terms of the probability of loss or injury occurring and the magnitude of the loss or injury if it occurs.
A simple procedure that can be used to determine risk involves developing a risk matrix for each hazard (see Table 1). Events that require first consideration are those events that occur most frequently and cause the most damage. Events that occur infrequently and that cause only minimal damage are least important to consider.
Table 1. Risk Hazard Matrix (Source: DHS’ National Protection and Programs Directorate and FEMA)
Severity | Probability of Occurrence | |||
Frequent | Probable | Occasional | Unlikely | |
Catastrophic | High Priority | High Priority | Middle Priority | Low Priority |
Critical | High Priority | Middle Priority | Middle Priority | Low Priority |
Marginal | Middle Priority | Middle Priority | Low Priority | Low Priority |
Negligible | Low Priority | Low Priority | Low Priority | Low Priority |
The purpose of performing this assessment is to rank potential hazards in terms of potential loss so that action and response priorities can be established. No company has unlimited resources: risk assessment allows companies to allocate the resources they do have most effectively.
Assess capabilities and resources
Once a hazard evaluation and risk analysis have been completed, the company’s preparedness, prevention and response capabilities need to be assessed. There are two types of resources to inventory: equipment and personnel. All equipment that can be used to prevent or respond to an emergency should be noted. This would include sprinkler systems, shovels, fire extinguishers, torches, spare parts, wheelbarrows, etc. A survey should be made of existing communications equipment, burglar alarms, fire detection equipment and any other emergency equipment. An inventory should be taken of medical equipment, first aid supplies, respirators and personal protective equipment. Equipment used to train personnel should be listed as well.
If the survey is done based on inventory logs, a physical inspection should be done to verify the equipment is available. When performing this review, it is important to also note the lack of required equipment. Once a complete review of equipment is accomplished, there will be a better idea on what equipment is available and what equipment is needed.
Employees on site, and their abilities, should then be assessed. This information will be very important for deciding what course of action should be taken before and during a crisis. As an example, a response to a fire will be different depending on the presence or absence of an organized fire brigade on site. Training programs can be implemented to train personnel.
Emergency planning
Having identified the potential hazards faced by the business and assessed the relative risk of their occurring, the next step in the process is to develop a written plan to cope with the occurrence of negative events. A separate emergency plan can be developed for each potential hazard; however, with separate plans, many elements of each plan will be the same or vary only slightly (e.g., rescue and medical duties, evacuation procedures, shutdown procedures, etc.). For this reason, it is generally recommended that a multi-hazard plan be developed.
A multi-hazard plan avoids unnecessary redundancy and confusion. It addresses the general elements of an emergency plan to cope with all hazards and then looks at each potential hazard to determine if there are any unique elements involved.
See Emergencies - Being Prepared Makes Business Sense on our Business Continuity page, for additional information.
Types of plans
There are four types of emergency plans commonly used in industry: action guides, response plans, emergency management plans and mutual aid plans.
- Action guide: An action guide describes, usually in a checklist format, the procedures to be followed in the event of an emergency. It outlines which company personnel and outside agencies are to be called, what information is to be collected and conveyed and other basic response functions.
- Response plan: Response plans, also referred to as contingency plans, describe the organization, responsibilities and procedures that will be initiated, and the equipment and facilities that will be required, should an emergency occur. Response-type plans provide information only on the actions that must be implemented to limit damage from an emergency; in general, they do not deal with pre-emergency or recovery planning. A specific response plan is usually developed for each hazard identified as high risk.
- Emergency management plan: This is a comprehensive program that includes the four phases of emergency planning, prevention, preparedness, response and recovery. It describes the methods utilized to prevent emergencies, the plans implemented to prepare for emergencies, the actions to initiate in the event of an emergency and the activities necessary to keep the organization functioning and to bring it back to full operation should damage be sustained. An emergency management plan should include response plans for each identified hazard.
- Mutual aid plan: A mutual aid plan is the plan developed by the participating firms in a mutual aid association in which they agree to share resources to assist one another in an emergency.
Developing the plan
Steps to be followed in developing emergency plans include:
- Review existing plans - The reasons for reviewing existing plans are twofold: to save on time and effort by building on or amending existing plans and to ensure proper coordination with the emergency plans of other organizations.
- Purpose of the plan - This will provide an outline of the company policy with respect to the occurrence of an emergency.
- Basis for plan execution - This section of the plan lists the potential hazards to the life and health of employees, to company property, and to the environment and includes a relative assessment of the risk that each hazard poses. It also identifies the conditions under which the plan is to be executed.
- Emergency response - For an emergency plan to be effective, the responsibilities of those involved in responding to an emergency must be clearly outlined.
- Emergency response structure - The number of personnel on an emergency response team depends on the size and on the complexity of the operations at the facility. The emergency response team should be under the direction of a team leader.
- Emergency response procedures - Once the responsibilities of the personnel on the emergency response team have been identified, the specific activities they will be required to perform in an emergency should be assigned. While many of the activities are common to all emergencies, other activities may be specific to a particular situation.
- Emergency response resources - Having selected the emergency response personnel and assigned their responsibilities, the next step is to identify the resources needed in responding to an emergency. This includes the establishment of an emergency headquarters, or command center, and identification of the vehicles and personal protective equipment (PPE) needed in the emergency response.
Writing the plan
Having completed the hazard identification and risk analysis, reviewed existing plans, and assessed prevention, preparedness and response capabilities, the next step is to write the plan if one does not exist or revise an existing plan to make it current.
Since emergency plans are used infrequently, they should be well-organized, concise, and easy to use. The plan should be indexed for ready reference and the pages numbered. Diagrams, charts, and checklists should be used to show the organization, summarize duties and responsibilities, and show how the organization should respond during normal and off hours.
See E&S Client Handout CH-45-08, Continuity of Operations – Critical Systems/Services Checklist, available through E&S on our Partners page, and Emergency Preparedness – Developing the Plan on our Risk Solutions Business Continuity page, for more information on how to develop a plan.
Protecting vital records
Vital records, those necessary to ensure the survival of a business, should be given maximum protection from every disaster. Indeed, for some businesses, the information contained in their records is the single most valuable asset. The loss of processing and trade secrets, drawings, formulas, and the like could easily end a prospering business.
Two questions should be asked of any company: “What records are vital?” and “What records must a company have to function?” This varies depending upon the type of business (i.e., manufacturing, financial, institutional, and so forth). However, there are certain fundamental records, such as the incorporation certificate, the bylaws, the stock record books, ownership and leasing documents, insurance policies, and certain financial records, vital to any corporate organization.
A manufacturing organization would, in addition, require engineering drawings and specifications, parts lists, details of work processes and procedures, lists of employee skills required, and similar information. Without these, it is impossible to produce a product. The task of recreating all this information following a catastrophe would be virtually insurmountable, especially for a complex product. A banking institution would require current information on the status of depositors' accounts, accounts with other banks, loan accounts, and related banking services.
Vital records can be classified into broad functional categories. These categories will be different in each company, but in general they should include:
- Finance: bill payment, account collection, and cost accounting.
- Production: research, engineering, purchasing, and related activities.
- Sales: inventory control and shipping activities.
- General Administration: personnel, legal, tax records, public relations, and similar staff information.
Vital records should be duplicated and updated on a regular basis, ideally with off-site storage of backup records. Vital records should be stored in the appropriate record protection equipment that is used only for such purpose. Contingency plans should be in place to retrieve and recover damaged records.
Data processing tapes and disks containing vital information should not be located in basement locations, to limit damage from floods, and stored in listed/approved record protection equipment. Backup copies of specialized software, as well as copies of critical data, should be stored at an off-premises location in the appropriate records protection equipment. Computer files should be backed up daily. Cloud storage of data should be protected in a secure environment.
Recovery operations
Recovery operations should not be overlooked when developing an emergency plan. Part of being prepared for an emergency is being able to quickly rebound from an unwelcome event and resume normal operations. Prior preparation will make recovery less difficult and probably more efficient. This will translate into smaller losses and less downtime.
Recovery operations should focus on two areas: salvaging property and assets and restoring business operations and production.
Salvage
Salvage of physical assets not only includes repairing or restoring items once damage has occurred; it also includes steps taken to prevent damage from occurring. Some emergencies, particularly those that are weather-related, provide sufficient warning to allow for advance action to be taken.
As soon as an emergency is recognized or forecasted, the following steps should be taken to make property and assets less vulnerable. These steps will help to minimize the extent of damage that may occur and reduce the amount of salvage necessary. Assure that:
- All sprinklers and loss prevention equipment are functioning properly.
- Stocks of supplies needed for salvage, such as tarpaulins, generators, wipe rags, oil, and rust inhibitor, are available and in working order.
- Damage-sensitive stocks and equipment are removed from danger-prone areas and protected, e.g., making sure water-sensitive products are skid-mounted and removed from flood-prone areas and possibly even protected by sandbags.
- Outside equipment is tied down to prevent wind damage.
As the emergency is occurring, steps can be taken to reduce losses. If an event is happening in a localized area in the facility, teams of employees can be used to remove physical assets from potential exposure areas and implement protection measures. An example of a localized emergency is flooding due to water-pipe rupture. Damageable assets in the water’s path can be removed or raised above expected flood level, and sandbags, boards, or other diking material can be used to limit the spread of the water to other areas.
Plans should be made for work that should be done once the emergency is over. Crews should be arranged for: assessing damage to structures and assets, performing temporary repairs to structures, performing maintenance or salvage on exposed equipment, separating out damaged from undamaged goods, etc. Suppliers, contractors, and specialty equipment restorers should be put on call for potential service. If extensive damage has been done, management should consider the possibility of moving equipment and supplies to temporary off-site storage or operating facilities.
Many decisions should be made quickly, and the required personnel may not always be available when an emergency is occurring. Planning is necessary to make sure that nothing important is forgotten and that steps are performed in priority order.
The first task that should be taken care of after an emergency is the assessment of the facility structure and the quick repair of any damaged protection equipment. For example, damaged sprinkler heads should be replaced and broken lines capped as soon as possible; fires have flared up and restarted after having been declared out.
Facilities should be checked for signs of any safety hazards that might injure employees or delay recovery. Such hazards include: unsupported walls, damaged floors or areas of potential structural collapse, leaky gas lines, live or exposed wiring, and dangerous chemicals or damaged gas cylinders. These hazard areas should be roped off, warnings installed, and steps implemented to remove the hazards. If a gas leak is suspected, personnel should be removed from the structure, the proper authorities notified, and the supply to the facility shut off, if possible.
Provisions should be made for making as much of the facility as weather-tight as possible. Roofs should be patched or covered with tarps, broken windows sealed, and doors repaired. Puddle water should be mopped up to limit moisture damage. Doors should also be secured to prevent looting. If an area requires extensive work, it might pay to remove important items to alternate locations on site and repair salvageable areas. Time should not be wasted on areas or equipment that cannot be saved.
Smoky or wet materials and equipment should be aired out and dried and damaged stock separated from undamaged stock. Damaged packaging should be removed to prevent damage to the enclosed product. These steps are required to prevent losses due to contamination. Secondary damage from smoke or moisture can be minimized with fast action.
Machinery that can be maintained on site should be disassembled, dried, oiled and reassembled. Electrical equipment, motors, controls, bearings, and close-tolerance tools and equipment are especially sensitive to water and heat. Machinery that requires special service should be sent back to manufacturers for rehabilitation. Electrical apparatus should never be reenergized until it has been checked out by a qualified electrician.
If large-scale damage has occurred, equipment repairs should be prioritized based upon what will help expedite recovery. Repairing a generator or hoist may aid recovery more than repairing a piece of production equipment. In an office environment, restoring a phone system or central computer is more important than repairing the copying machine.
Restoring business operations and production
Quick resumption of business operations is paramount for minimizing losses. If a business is not producing, it is not generating revenue. No business can survive long this way. Extended downtime can result in the loss of furloughed employees. It can also result in loss of customers to alternate sources. Remember that no product/service is irreplaceable. The misfortune of one company can be the opportunity of another.
The three keys to restoring business operations include making sure that:
- Vital business records are kept intact and damage-free.
- Key production equipment is quickly restored.
- A location can be provided where operations can take place.
Vital records must be made safe. These include: accounting records, business contracts, insurance policies, equipment diagrams and specifications, production line specifications, operating parameters, product tolerances, vender information, certificates of incorporation and tax numbers. Companies must know who they supply, who supplies them, who they owe, who owes them, what they produce, how they produce it, etc. Loss of plans, specifications, and instructions can delay or prevent a recovery while the product and production scheme are being reinvented. Natural Hazards Report NH-30-14, Emergency Preparedness – Protecting Vital Records on our Business Continuity page, provides guidelines for setting up a records protection program.
Key production equipment that has been damaged must be repaired quickly. Quick restoration will depend heavily on the ability of a company to detail the specifications of their equipment. Many production lines develop or modify production equipment to fit their assembly line. Records of these designs or modifications must be kept so that equipment manufacturers can restore or rebuild equipment to proper specifications.
When recovery planning is done, the possibility of total loss of production should be considered. In this case, the company should weigh the benefits of rebuilding versus modifying the production scheme. Either way, plans and specifications should be made beforehand, so that recovery operations are not delayed by indecision.
Repairs, particularly extensive repairs, may take a while to complete. If a company owns or operates more than one facility, employers should consider emergency relocation of workers and equipment to these other facilities. Temporary production lines can be set up or extra shifts added. Goods can be shifted to alternate warehouses. If a company does not own another location, short-term leasing should be considered.
To expedite repair, companies should develop contacts with contractors, planners, and designers. Names and numbers of these people should be kept on hand, so those repairs can be swiftly implemented. By having prior contacts established, no time will be wasted "auditioning" talent, and if the emergency has affected a large area, the relationship may result in obtaining preferential service as a repeat customer.
Fire protection
Since fire is one of the most frequent emergencies facing businesses, particular attention should be given to fire protection. Factors that should be considered to control the risk of business interruption from fire include:
Building construction
The facility should comply with local building and fire prevention codes. While codes can vary widely from state to state, some basic measures are common to all codes. These include: fire exposure from adjoining facilities or adjacent structures should be limited by fire barriers or building separation; concealed spaces should be properly fire stopped or otherwise protected; and in multiple-story buildings, floors should be constructed to act as smoke barriers and vertical openings protected to prevent the spread of smoke and fire.
Utilities
The electrical system should comply with NFPA 70, National Electrical Code, published by the National Fire Protection Association (NFPA). Some basic requirements of NFPA 70 include: electrical conductors should be securely fastened in place; outlet and junction boxes should be properly secured, covered, and without evidence of overheating; wiring insulation in outlet and junction boxes should be in good condition and not frayed or loose; an adequate number of electrical outlets/circuits should be provided to avoid overloading of circuits; the use of extension cords should be prohibited; electrical panels and branch circuit disconnects should be freely accessible at all times; and all electrical equipment should be inspected and maintained according to manufacturer’s instructions.
Heating and air conditioning systems should comply with NFPA 90B, Standard for the Installation of Warm Air Heating and Air Conditioning. Air circulation systems should be designed to automatically shut down in the event of a fire. Proper maintenance of these systems will help to prevent overheating of motors, which could result in fires. Other factors to be considered include: (1) heating systems should be in a separate area with a minimum fire-resistance rating of two hours and having no opening within 10 ft (3 m) of flammable liquid storage; (2) return air for heating systems should be at least 18 in (45.5 cm) above the floor; and (3) return-air supplies should not be drawn from maintenance shops or other areas where flammable liquids are used or stored.
Gas- or oil-fired equipment should be provided with a manually-operated, emergency shutoff valve for the fuel supply. These valves should be prominently located, preferably outside the area of the operation. Gas service should comply with NFPA 54, National Fuel Gas Code. Control valves for gas service should be readily accessible and in good working condition.
Storage areas
Consumable supplies should be stored in conformance to local fire code requirements and follow good storage practices. The specific types of storage practices will depend upon the supplies and storage arrangements, as follows: (1) supplies should be stored on stable surfaces, in stable configurations, and should not block access to fire and emergency exits; (2) adequate aisles/spacing should be provided to limit congestion, prevent the spread of fire, and provide for firefighting access; (3) ordinary combustible materials, such as records, tools and paper supplies, should be stored separately from flammable liquids; (4) supplies and stock should be located at least 3 ft (0.9 m) from heating units and duct work; and (5) storage rooms, trash rooms, and similar areas should be separated from other areas by one-hour fire barriers or protected by automatic sprinklers.
Flammable and combustible liquids should be kept in covered containers when not in use. Spills should be cleaned up promptly. Flammable and combustible liquids should be stored in accordance with NFPA 30, Flammable and Combustible Liquids Code. Storage rooms containing flammable or combustible liquids should be segregated by fire barriers and protected by automatic sprinkler systems. Inside storage should be limited so that not more than 120 gal (454 l) of flammable or combustible liquids are stored in any one cabinet and not more than three cabinets are located in the same storage area. In addition, storage areas should be (1) provided with spill-containment devices; (2) provided with electrical equipment that is approved/listed for a Class 1, Division 1 use; and (3) equipped with ventilation equipment designed to maintain a constant flow of air to prevent the buildup of flammable vapors.
Special consideration should be given to the storage of corrosive liquids. Building maintenance activities use a variety of corrosive liquids, such as toilet bowl cleaners and floor strippers. These liquids should be stored separately from flammables, either in corrosive-liquids’ cabinets or in a room specifically designed for that purpose. Automatic sprinkler systems should be used to protect all chemical storage areas, and spill-containment devices should be provided.
Fire alarm system
A fire alarm system should be designed, installed and maintained in accordance with requirements of NFPA 72, National Fire Alarm Code. The system should be monitored by a central station alarm company, with automatic retransmission of fire alarm signals to the fire department. NFPA 72 requires that a fire alarm system be covered by a maintenance and service contract and regularly tested and inspected.
The system should include both manual and automatic initiation devices that provide immediate evacuation notification to the occupants. A voice communication system should be installed to notify customers of an emergency and provide directions, as necessary. Fire suppression systems for commercial cooking equipment should be equipped with alarms that are integrated into the building alarm system. Activation of the system should cause the release of hold-open devices on smoke compartment doors.
Fire suppression systems
The facility should be protected by an automatic fire sprinkler system meeting the requirements of NFPA 13, Standard for the Installation of Sprinkler Systems. Requirements for maintaining sprinkler systems are contained in NFPA 25, Standard for the Inspection, Testing, and Maintenance of Water-based Fire Protection Systems.
Fire extinguishers should be located throughout the facility, in compliance with local codes and as required by NFPA 10, Standard for Portable Fire Extinguishers. Employees should be trained in the care and use of these extinguishers, including proper selection and application for the classes of fire presented.
Properties located in areas without public water systems should be protected by alternate water sources, in accordance with NFPA 1142, Standard on Water Supplies for Suburban and Rural Fire Fighting.
Smoking
Smoking should be prohibited in the facility. If smoking is permitted, designated smoking areas should be established and “No Smoking” signs should be posted in all other areas of the facility. Improperly discarded smoking materials, such as cigarettes, can ignite combustible waste. Non-combustible receptacles for smoking materials should be provided and routinely emptied by the staff.
Improperly discarded smoking materials, such as cigarettes, can also ignite combustible waste in outside areas. Receptacles for smoking materials should be placed outside the facility, especially if smoking is not permitted inside. Wood chips and mulch should be kept away from the building so that a discarded cigarette does not ignite an exterior fire.
Housekeeping
Used cardboard cartons and packing and crating materials can accumulate in stock rooms, increasing the fire load in such areas. To minimize the danger of fire, stock rooms should be tidy and orderly and trash should be removed to an outside trash dumpster or otherwise disposed of. Storage rooms, trash rooms, inside dumpsters, and similar areas should be separated from other areas by one-hour fire barriers or protected by automatic sprinklers.
Incendiarism and arson
Basic protection against incendiarism and arson requires that the property be secured from unauthorized entry and equipment protected. A fence may be used to protect the perimeter of the property. All exterior areas of the property should be illuminated. Trees and vegetation should be cut back to provide a clear space of at least 100-ft (30.5-m) clearance around the perimeter of the property. Combustible materials and trash in yard areas should be properly discarded. Deadbolt locks should be installed on all exterior doors. Ground-level and below-grade windows, and other accessible openings, should be secured. Lockable gas caps should be provided for motorized equipment.
See E&S Fire Protection Report FP-42-01, Incendiarism and Arson, and Crime Prevention Report CP-30-10, Physical Protection Afforded by Buildings on our Risk Solutions Partners section, for additional information on these topics.
Summary
While businesses cannot totally prevent the occurrence of disasters, the keys to controlling business interruption losses are to have plans in place to prevent or limit damage from a disaster and, in the event of a shutdown, to return the business to operation as soon as possible. This requires that a business have an emergency preparedness plan.
Each business has circumstances and structures that are unique, so a plan will have to be tailored to suit its needs. It is important to recognize that there is no “magic” plan that a company can purchase that will provide all the answers or that will create a plan for them. There is no document that will address every situation and circumstance. Planning for and controlling business interruption exposures requires a company’s leadership team to identify, assess, and prioritize various exposures that could lead to property damage or an inability to maintain business operations. Once the exposures are identified, the team can develop strategies to limit damage or protect against disaster.
Emergency preparedness planning is essential for successfully minimizing any adverse effects of an emergency or disaster on a business and its operations. The plan should be designed to limit potential damage to keep the business operating or, in the event of a closing, to bring it back to operation as soon as possible.
References
- Engineering and Safety Service. Emergency Response – An Overview. NH-30-10. Jersey City, NJ: ISO Services, Inc., 2008.
- ––. Emergency Response – Developing the Plan. NH-30-11. Jersey City, NJ: ISO Services, Inc., 2016.
- ––. Emergency Response – Recovery Operations. NH-30-13. Jersey City, NJ: ISO Services, Inc., 2008.
- U.S. Department of Homeland Security. Ready Business Mentoring Guide – Preparing Small Businesses for Emergencies. Washington, DC: DHS, 2011. https://www.fema.gov/media-library-data/1392217307183-56ed30008abd809cac1a3027488a4c24/2014_business_user_guide.pdf.
To learn more about Hanover Risk Solutions, visit hanoverrisksolutions.com
Copyright ©2018, ISO Services, Inc.
The recommendation(s), advice and contents of this material are provided for informational purposes only and do not purport to address every possible legal obligation, hazard, code violation, loss potential or exception to good practice. The Hanover Insurance Company and its affiliates and subsidiaries ("The Hanover") specifically disclaim any warranty or representation that acceptance of any recommendations or advice contained herein will make any premises, property or operation safe or in compliance with any law or regulation. Under no circumstances should this material or your acceptance of any recommendations or advice contained herein be construed as establishing the existence or availability of any insurance coverage with The Hanover. By providing this information to you, The Hanover does not assume (and specifically disclaims) any duty, undertaking or responsibility to you. The decision to accept or implement any recommendation(s) or advice contained in this material must be made by you.
LC DEC 2018-395
171-10021 (11/18)