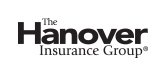
Cargo theft prevention and risk mitigation for the holiday season
As the holiday season approaches, manufacturers' warehouses are packed to capacity as high-season inventory begins to make its way into the stores and onto the shelves.
This is the time of year when product moving through the supply chain is the most vulnerable.
This vulnerability is not because security efforts have become careless; it's because of greater volume. We are shipping more to meet consumer needs, therefore, cargo thieves have more chances to steal from us.
Despite the rising security threats, you do not have to be a victim of cargo theft.
You can successfully mitigate your company's cargo theft risk by taking two important steps.
- Understand where and how cargo thieves operate.
- Add several precautionary measures to your security protocol before, during and after a load leaves your facility.
During the holiday season most theft incidents occur when product is en route from a factory or warehouse to a distribution center or retail store.
Special planning and preventive measures need to be put in place long before product is given to a driver and released out onto the open road.
Preventive analytics can help your company carefully plan the safest routes for your goods, from origin to destination.
Historical cargo theft data can help your company determine the best routes to take, cities to travel through, and truck stops to use. By doing some homework, your company can significantly reduce the risk of cargo theft by "thieves of opportunity," who tend to be somewhat territorial, operating along the same roads and around the same rest areas daily.
Carrier selection
Before moving any cargo, consider your carrier choice carefully.
You should interview and make sure they can demonstrate that they follow industry security best practices, such as background investigations on all of their drivers.
Each driver who works for a carrier that your company uses should be educated on how to prevent cargo theft, and in the event of a theft, procedures to follow immediately.
When hauling a load for your company, drivers should:
- Notify their dispatcher if/when they plan on stopping.
- Always arrive at your facility with full tank(s) of fuel.
- Always drive a minimum of 250 miles after accepting one of your loads before stopping.
- Only use "approved" rest stops along their route.
- Park their trucks in an area where other drivers are present when stopping.
- Drive in two-person teams (if possible).
- Never leave the vehicle unattended (if possible).
- Never take the load home or park in unsecured areas.
- Keep tractor windows up and doors locked when traveling at low speeds or stopping.
- Keep important information concerning the tractor and trailer (VIN, license plate numbers, trailer numbers, a description of the trailer) on themselves at all times.
- In the event of a theft, contact the local police, notify your company's supply chain group, their dispatcher, etc.
Your carrier should also agree to provide you with the identity of the driver picking up your load at least 24 hours prior to when the product is due to leave the loading dock. This identity should be confirmed when the driver arrives at the in-gate of your facility.
The carrier should also agree that they will NOT subcontract any jobs surrounding your shipments. This is important because cargo thieves will set up fictitious companies and post low rates on load-boards to "legally" acquire access to shipments.
By not vetting your carriers prior to shipment, you run the risk of potentially handing over your inventory to thieves.
Physical security
Your shipment, which could be worth hundreds of thousands of dollars, will travel on open roads while being looked after by one or possibly two people, so the physical security of a conveyance is very important.
Physical security devices such as seals and GPS tracking devices will not keep a determined cargo thief out, but they can deter a thief who may see your cargo as a target of opportunity while parked in a rest stop.
High-security barrier seals from a reputable manufacturer whose seals adhere to standards set forth by ISO/PAS 17712 are your best bet.
Your company should evaluate the type of security seals that they use to keep cargo secure while between facilities. Bear in mind that all security seals are meant to be opened, and, therefore, security seals are more of a deterrent than a barrier to entry. On trailers with "barn-style" doors, it has been recommended to use 3/16" steel cable seals that are long enough to wrap around both locking bars and be cinched-up tight. Using a cable seal like the one mentioned will prevent the left door from being opened during transit without compromising the seal. On trailers with "roll-up-doors," a 3/8" steel bolt seal should be sufficient. Seals should be applied at the out-gate of your facility by corporate security personnel, and not by the driver. Seal numbers should be recorded, acknowledged by the driver, and forwarded electronically to the in-gate personnel at the destination facility for examination upon arrival.
Another layer of over-the-road security that you should consider using is GPS tracking.
It is important that your company knows where their load is at all times both for security and logistics purposes. Your carrier may tell you that they track every shipment they haul through the use of a satellite tracking system mounted in/on the tractor. While this type of system does have its merits, it is designed to track truck diagnostics, truck location, and driver behavior—not the trailer or cargo inside the trailer. Also, one of the first things that cargo thieves do when stealing a load is make this type of device inoperable by covering, disconnecting, or destroying the satellite antenna.
GPS tracking technology has come a long way over the past few years. GPS tracking devices were once large and cumbersome, and they required an antenna to be mounted on the outside of the shipping conveyance. Due to the high price tag, GPS tracking was seen only as a tool for companies moving extremely valuable product. They were not used in the mainstream commercial market.
GPS tracking devices are now smaller, less expensive and don't require an external antenna. They can be covertly packed within a pallet, have battery capacity long enough to last a month and are smart enough to tell the end-user when and if there is a problem. There are numerous benefits of using GPS tracking to remotely monitor your company's cargo, including being alerted if your cargo sits in one location for too long (remember: cargo at rest is cargo at risk), being alerted if the conveyance is opened, and being alerted if the conveyance containing your cargo deviates from a predetermined route. If the cargo containing a GPS tracking device is stolen and your company is using a reputable monitoring service, the police in that particular jurisdiction can be given the exact location of the stolen cargo in hopes that they can recover it quickly.
Before you ship
When the carrier arrives, employees working the gate need to inspect the vehicle and trailer and record important information about the driver, tractor, and trailer, which can be used later in the event of a theft.
The integrity of the tractor and trailer are important. The first thing to look at is the overall appearance of the tractor. Does the truck have large amounts of rust on the body? Does the tractor contain a large amount of fiberglass damage? Does the tractor need new tires? Does the tractor look over-used or dilapidated? If your employees can answer 'yes' to any of these questions, do not allow the truck to haul your shipment. Rust, fiberglass damage and balding tires could be an indication that this truck has not been properly cared for, which could result in a break-down along its trip. When a truck carrying your product breaks down, there is a chance that it could sit on the side of the road for several hours before being transferred to another truck to continue its trip. Once again, the adage applies, "Cargo at rest is cargo at risk."
Next, your gate staff should inspect the trailer. Is the roof of the trailer damaged? Is its floor not entirely intact? Are the rubber seals around the trailer's door edges not fully present? Do the doors have problems closing and sealing properly? Are the trailer's tires in bad condition? Are all of the lights on the trailer not functioning? If your gate staff can answer 'yes' to any of these questions, send the driver away. Roof damage, floor damage and door issues could be an indication that the trailer has not been properly cared for, which could result in a break-down. Also, it is not a good practice to transport product inside trailers damaged by over-use, neglect, or bridge collisions because of the possibility of damage to the product.
The driver needs to be able to travel at least 250 miles before stopping for any reason, including re-fueling.
If the tractor and trailer passes muster, gate staff should then check the level of the tractor's fuel tanks. If the fuel tanks are anything but full, send the driver to top-off his or her tanks before returning to pick up the shipment. The reason for this is because historical crime data has shown that a significant amount of cargo thefts occur within 250 miles of the origin facility.
Important information
Important information needs to be recorded before the driver can leave your facility while hauling one of your loads. The information collected must be kept in an easily accessible place (e.g., corporate intranet, shared network drive, etc.) in the event that the load is stolen while en route to the intended destination.
Some of the collected information should also be given to the driver with explicit instructions to keep it on his or her person at all times.
The first section of information that needs to be collected concerns the driver.
Information concerning the individual moving your freight must be recorded. It is critical to be able to connect a name to a face in the event of an incident. Making such a connection may require processes and protocols to tie themselves together via some legacy or third party software.
The second section of information that needs to be recorded regards the tractor and trailer.
Photographs of the tractor and trailer should be taken from the side and rear. Tractor and trailer information should be recorded, including Vehicle Identification Numbers, license plate numbers, year/make/model of each and a written description of each. A printout of this information should also be given to the driver along with important instructions to follow in the event of a cargo theft incident (i.e., first call the police, then call your contact person).
By arming your carrier and your company with important information about the driver, tractor, and trailer, you significantly increase your chances of recovering cargo if it is stolen.
Typically when a trailer full of cargo is stolen from a truck stop, law enforcement need more details than they receive. There are thousands of "white trailers with writing on the side" operating daily on this country's interstates. By being able to provide the police with actual license plate numbers and full vehicle descriptions immediately, they know exactly what they are looking for.
Post shipment
Finally, after a shipment has left the facility, there is still work that needs to be done.
All information that was collected at the gate, such as relevant driver information and truck/trailer information must be placed into a folder and catalogued electronically.
This information must be able to be accessed quickly and easily in the event of a theft.
Your company needs to have guidelines in place as to how to react in the event of a cargo theft incident. If the supply chain person "on-call" one evening gets a call from the driver at 11:30 p.m., that person should know exactly whom to contact, how to transmit relevant data and how to get the alerting and recovery process started (if applicable).
In conclusion, cargo theft risk can be mitigated by using a few preventive measures including:
- Preventive analytics
- Carrier selection
- Driver education
- Physical security
- Information recording
Source: CargoNet, a division of ISO, a leading source of information about property/casualty insurance risk.
To learn more about Hanover Risk Solutions, visit hanoverrisksolutions.com
The recommendation(s), advice and contents of this material are provided for informational purposes only and do not purport to address every possible legal obligation, hazard, code violation, loss potential or exception to good practice. The Hanover Insurance Company and its affiliates and subsidiaries ("The Hanover") specifically disclaim any warranty or representation that acceptance of any recommendations or advice contained herein will make any premises, property or operation safe or in compliance with any law or regulation. Under no circumstances should this material or your acceptance of any recommendations or advice contained herein be construed as establishing the existence or availability of any insurance coverage with The Hanover. By providing this information to you, The Hanover does not assume (and specifically disclaims) any duty, undertaking or responsibility to you. The decision to accept or implement any recommendation(s) or advice contained in this material must be made by you.
LC FEB 2019 10-437
171-1005 (1/14)