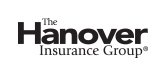
Backhoe and hydraulic excavator safety
This advisory provides some of the guidelines established for backhoe and excavator operators by the American Pipeline Contractors Association in alliance with the Occupational Safety and Health Administration (OSHA), the National Institute for Occupational Safety and Health (NIOSH), and the Association of Equipment Manufacturers. The handout does not cover all backhoe and excavator operations, nor does it address trenching and excavation safety in general.
Pre-operation
- Maintain required separation distances between equipment and power lines as mandated by federal, state, and local regulations, and as issued by authorities having jurisdiction. See 29 CFR 1926.600(a)(6) for OSHA regulations.
- Use a spotter for hard-to-see separation distances and for all other utility installations or tight conditions.
- Before each work shift begins, review and confirm communication signals between machine operators and affected workers.
- Only qualified personnel shall operate equipment.
- Read, understand and follow the operator’s manual; consult the manual to determine the maximum allowable slope for safe operation.
- Wear appropriate personal protective equipment (PPE) as required by the task being performed, company policy and OSHA and applicable regulations.
- Verify the fire extinguisher location. Check and verify it is operational and make sure you are qualified to operate it.
- When refueling, bond the supply tank with the fuel tank to prevent static discharge and possible fire.
- Conduct a walk-around inspection checking all fluids and noting any items needing maintenance and repair. Ensure repairs are conducted prior to operation.
- Make sure all warning labels are legible. Those not legible must be cleaned or replaced.
- Ensure that bucket teeth are barred if working around underground utilities. Barring is the installation of a steel plate or bar over the exposed area of teeth of the bucket so that no area of the teeth protrudes.
- Use the CALL BEFORE YOU DIG (dial 811) One-Call nationwide notification system to locate underground utilities. Ensure that utilities are marked and depth is verified before the commencement of digging activities. All utilities shall be located by hand before the use of backhoes and excavators.
- Verify that any attachments that have the quick couplers are properly connected to prevent accidental disconnect which could cause injury or death to personnel.
- Get on the machine only at locations that have steps and/or handholds. Use three points of contact to enter the machine. If the machine does not have these, advise your supervisor immediately. Do not use any controls as handholds when entering or exiting the operator compartment.
- Remove debris and clutter in the cab that would prevent safe operation.
- Check to ensure the seat belt is operational. Always use the seat belt when operating the piece of equipment.
- Use the rollover protection system (ROPS) supplied by the manufacturer.
- Check that controls are in proper settings before starting machine. Under no load perform a pre‐operation function check to verify proper operation of equipment, including verification of back up alarm.
Operation
- Verify that the One Call has been made and that utilities are marked, and depth verified before the commencement of digging activities.
- Mats shall be used on soft ground, wet lands and at other times when needed.
- No personnel shall be under the bucket or the backhoe while it is being raised or lowered.
- When the equipment is in operation, the doors (when installed) must be closed or secured by latch in the open position.
- Travel on steep grade shall be straight up and down vs. sideways. Follow manufacturer’s recommendations.
- When necessary to park on a grade, do so according to the manufacturer’s recommendations.
- Verify that the machine is level with stabilizing feet and the front bucket down when digging.
- Equipment shall be kept as far away as practical from the side of the excavation.
- Verify that enough room is available to keep spoil pile at a safe distance from the side.
- All unnecessary personnel shall be prohibited from the work area.
- Ensure there is room for the swing radius and bucket operation.
- Ensure there are no obstructions or ground people in the swing radius. Keep workers outside swing areas by marking them with rope, tape, or other barriers.
- When moving equipment, the bucket shall be lowered and curled in.
- Be aware of suspended loads, counterweights, and pinch points. Workers should maintain eye contact with the operator at all times.
- Hand signals shall be given by one person and must be understood by all personnel on site.
- When moving a load, proper rigging and lifting and techniques shall be used.
- No riders shall be permitted, and no personnel shall be lifted or carried in the bucket.
- If the operator leaves the seat of the equipment, the hydraulics shall be lowered to the ground. Set parking brake, chock and block if necessary, and turn the machine off.
- Do not operate this piece of equipment during stormy conditions. Seek shelter according to the company’s emergency action plan.
Post-operation
- Park, set parking brake and chock and block as necessary.
- Lower all hydraulics and set hydraulic lock out.
- Shut engine off, remove key, lock doors and engage security system (if available).
- Use three points of contact to exit the machine.
To learn more about Hanover Risk Solutions, visit hanoverrisksolutions.com
Copyright ©2019, ISO Services, Inc.
The recommendation(s), advice and contents of this material are provided for informational purposes only and do not purport to address every possible legal obligation, hazard, code violation, loss potential or exception to good practice. The Hanover Insurance Company and its affiliates and subsidiaries ("The Hanover") specifically disclaim any warranty or representation that acceptance of any recommendations or advice contained herein will make any premises, property or operation safe or in compliance with any law or regulation. Under no circumstances should this material or your acceptance of any recommendations or advice contained herein be construed as establishing the existence or availability of any insurance coverage with The Hanover. By providing this information to you, The Hanover does not assume (and specifically disclaims) any duty, undertaking or responsibility to you. The decision to accept or implement any recommendation(s) or advice contained in this material must be made by you.
LC APR 2019-292
171-0833 (6/19)