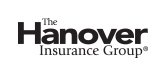
Air supported structures
Air supported structures, commonly referred to as “bubbles,” are typically used to provide protection from the elements for tennis courts, swimming pools and athletic fields. Properly installed and maintained, they can provide a low cost alternative to other building types. From a loss control perspective, owners of air supported structures should have specific procedures in place to reduce the possibility of structural failure due to covered perils.
Structure types
The concept of an air supported structure is based on maintaining air pressure within the fabric envelope slightly higher than exterior air pressure. This keeps the fabric upright and stable. Larger “dome” structures, used for sports stadiums, have a fabric roof anchored to exterior walls. Smaller structures have fabric anchored to a concrete lip set in the ground. Each manufacturer has its own design and construction methods, but generally all bubbles tend to have four basic components:
- Fabric Membrane – Typically synthetic polyester or fiberglass, coated with PVC or Teflon formulation, for resistance to ultraviolet light and to improve fire resistance. Depending on the design, the fabric can have an embedded network of steel or fabric cables for additional anchoring strength.
- Pressurization – A combination of high output fans and HVAC equipment to maintain pressure and interior temperature. Backup is required in the event of a single fan failure. Additionally, an emergency generator should be installed for use during a power failure.
- Egress – Airlock type doors to provide entrance and exit paths. National Fire Protection Association (NFPA) Life Safety Code 101 requirements apply to the number and size of doors.
- Lighting – Bubbles have fairly good light transmission to the interior during daylight. Lighting can be added and can be either fixed at the interior sides or suspended from the membrane.
Maintenance
Proper maintenance and attention to snow
loading are key factors in preventing an air
supported structure collapse. Specific actions
to prevent collapse vary by structure type
and manufacturer. Refer to manufacturer’s
maintenance requirements and procedures
to prevent snow load induced failure. Blizzard
conditions, or wet snow combined with
little or no wind, can cause significant snow
loading in a short period of time.
Manufacturers’ snow removal recommendations
should be followed. Guidelines will
likely include the following:
Increase internal air pressure and/or temperature, according to the dome manufacturer’s procedures, to cause the snow to break up and slide off. A drag rope can also be used, where specified by the manufacturer, to loosen and break up frozen snow on the exterior. |
Remove snow buildup from the sides of the structure to eliminate side pressure. Blizzards compound this by creating drifts on the windward side of the structure. During snow removal give specific attention to areas where the fabric joins fixed, standing objects such as HVAC systems and exit doors. |
Provide scheduled maintenance of the blower inflation system for proper operation. |
Develop winter storm contingency plans, monitor weather forecasts and have staff available, when needed. |
Lower interior equipment and lights during heavy snow storms. |
Keep the back up generator on a maintenance test schedule. |
Follow manufacturer’s requirements during seasonal take down and installation of the structure. |
NFPA 102 requires an annual inspection of the structure plus any required maintenance. A biennial inspection of the structure by a professional engineer, registered architect or an individual certified by the manufacturer is also required by NFPA.
Fabric life span
Fabric life span varies with weather, sun exposure, quality and maintenance. Ten to 15 years is typical. The biennial inspection may result in recommended fabric replacement depending on condition.
Other requirements
- Surrounding vegetation or other combustible materials within 10 feet of the structure should be cleared.
- LPG tanks, where used, should be located no less than 5 feet from the structure. Tanks or gas lines should be protected from vehicular traffic.
To learn more about Hanover Risk Solutions, visit hanoverrisksolutions.com
The recommendation(s), advice and contents of this material are provided for informational purposes only and do not purport to address every possible legal obligation, hazard, code violation, loss potential or exception to good practice. The Hanover Insurance Company and its affiliates and subsidiaries ("The Hanover") specifically disclaim any warranty or representation that acceptance of any recommendations or advice contained herein will make any premises, property or operation safe or in compliance with any law or regulation. Under no circumstances should this material or your acceptance of any recommendations or advice contained herein be construed as establishing the existence or availability of any insurance coverage with The Hanover. By providing this information to you, The Hanover does not assume (and specifically disclaims) any duty, undertaking or responsibility to you. The decision to accept or implement any recommendation(s) or advice contained in this material must be made by you.
LC Jan 2019 10-08 H
171-0895 (1/14)